TEACHING MATERIALS for Students
2. New technologies for textile functionalization
2.7. Layer by Layer deposition
Layer-by-Layer (LbL) is a thin film fabrication technique. The films are formed by depositing alternating layers of oppositely charged materials. The layers can be performed in different ways e.g. dip coating, spin-coating, spray-coating. Various materials can be deposited by LbL method including polyions, metals, ceramics, nanoparticles, and biological molecules.
The LbL assembling can be qualified as a good alternative approach to the well-known deposition methods, because it is versatile, inexpensive, and comfortable for use. The large advantage of LbL method is that is suitable for the formation of a uniform coating on curved surfaces. The whole process of multilayer structures buildup by LbL assembling, whose driving force, despite hydrogen bonding, covalent bonding, etc., is mainly electrostatic interaction between the oppositely charged species, usually consists of four steps (see Figure):

The applied positively charged polyelectrolytes are: polyallylamine hydrochloride (PAH), polyethyleneimine (PEI), polydiallyldimethylammonium chloride (PDDA),
The applied negatively charged polyelectrolytes are: polyvinyl sulfate (PVS), polyacrylic acid (PAA), or polystyrene sulfonate (PSS).
The LbL method is appropriate to obtaining organic/inorganic films with high accuracy by changing the number of multilayers, concentration and pH of the solution.
Today, the LbL self-assembling technique is an effective process to design drug delivery systems, capacitors, sensors, solar and fuel cells, quantum dots, catalysts with unique properties, using metal nanoparticles (Au, Ag, Pd, Pt), metal oxides incorporated into appropriate polymer. Such metal nanoparticles with attractive optical, electronic, and catalytic properties are used in a broad range of applications ranging from physics to medicine.
Source: Thin Film Processes - Artifacts on Surface Phenomena and Technological Facet, Chapter 8, InTech Open.
A) Application of LbL method for preparing silica shell
LbL method is used for preparing silica shell with silica nanoparticles coated alginate microparticles by adding binder (PDDA), see on the Fig. 2.7.2 bellow - on scheme.
Fig. 2.7.2 Scheme of LbL deposition
Mechanism: producing of silica-coated alginate particles with specific controllable shell structure for applications in drug and other chemicals delivery. The silica shell is made by electrostatic Layer by Layer assembly of silica nanoparticles on the surface of alginate microparticles which are negatively charged as well as silica nanoparticles. The positively charged polyelectrolyte Polydimethyldiallylamonium chloride (PDDA) is used as a “binder”.
Dip coating method was used with following steps:
- PDDA (positively charged)
- Washing
- Silica np (negatively charged)
- Washing
Steps from 1. to 4. are repeated untill the functional coating reachs the desired thickness.
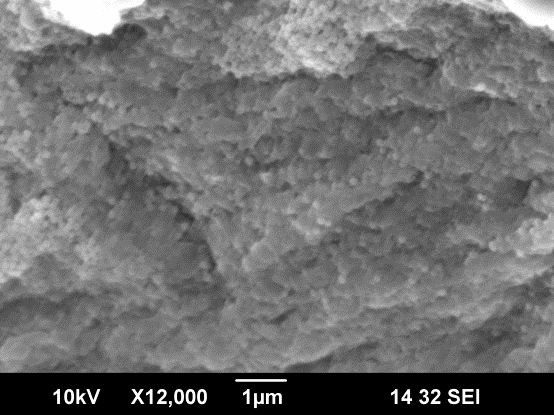
Fig 2.7.3 SEM image of silica np deposited on alginate particle Fig 2.7.4 Thickness of (PDDA/silica np) layers calculated from the QCM (by Quartz Crystal Microbalance) measurement.
Source: Layer-by-Layer method – Chobotix
Useful link:
B) Application of LbL method on textile substrate
Application of LbL method on textile materials in recent time considered as promising technique in achievement functional coatings on textile materials and attract great attention of different scientists.
Mechanism:
Research group consist of scientist from University of Science and Technology of China, are used the layer by layer (LbL) deposition of chitosan/melamine/urea (CS/ME/UREA) and phytic acid (PA) onto the acrylic acid (AA) grafted Polyamide 6.6 (PA 6.6) fabrics including a pad-dry-cure treatment with chitosan/graphene oxide (CS/GO) nanocomposites were considered to improve the hydrophilicity and durable flame retardancy, see schematic representation reaction below:
Fig 2.7,5 Schematic representation reaction of functional coatings on textile materials
Testing methods:
- Limiting oxygen index (LOI) value for flame retardancy,
- Melt dripping tendency,
- Peak Heat Release Rate (pHRR)
- Thermogravimetric analysis (TGA) test for thermal stability and char yield%,
- Hydrophilicity,
- Hybrid coatings stability after 10 home laundering cycles
Results:
- Hybrid coatings significantly improve the flame retardancy as the limiting oxygen index (LOI) value reached up to 25% from 18.5%,
- Completely stop the melt dripping where the fabric sample with two bilayers (2BLs) deposition and simultaneously treated with CS/GO nanocomposite (PA6.6-g-AA-2BL-CS/GO) achieved a V-1 rating.
- Two blayers (2BLs) deposited hybrid coating (i.e., PA6.6-g-AA-2BL-CS/GO) decreasing the Peak Heat Release Rate (pHRR) by 47.1%; a maximum reduction of pHRR by about 56% was achieved for five bilayers (5 BLs) deposition.
- Considerable improvement in thermal stability and char yield% were also realized in the thermogravimetric analysis (TGA) test. Furthermore, the as-prepared hybrid coatings imparted better hydrophilicity as a 2BLs deposition along with pad-dry-cure treatment by CS/GO could boost up the hydrophilicity of the treated fabrics further compared to the only 2BLs deposited fabric sample.
- Hybrid coatings could withstand against 10 home laundering cycles.
Source: M. Ziaur Rahman et al: Progress in Organic Coatings,144, Juy 2020, accessed at: https://doi.org/10.1016/j.porgcoat.2020.105640
Useful link: Cholesterol biosensors prepared by layer-by-layer technique, Biosensors & Bioelectronics 16 (2001) 849–856