TEACHING MATERIALS for researchers/teachers trainees
2. New technologies for textile functionalization
2.9. Mechanical treatments and auxetic materials
2.9.1. CalenderingTextile materials undergo mechanical processing by calendering under controlled conditions of heat and pressure, with the purpose of achieving different textures or effects in the fabric - the result: a more compact and flat fabric with a smoothing effect (smoothness).
Fig. 2.9.1. Calendering prpcess; schematic representation
Biopolishing
👉 1-s2.0-S0141391022000878-gr3_lrg.jpg (2917×3498) (els-cdn.com)
Source: A review on microplastic emission from textile materials and its reduction techniques - ScienceDirect
Read more in Critical Review on Sustainability in Denim: A Step toward Sustainable Production and Consumption of Denim | ACS Omega
2.9.2. Auxetic materials - helical auetic yarn (HAY)
Auxetic textiles have advanced rapidly in the past few decades due to their intuitive behavior of expanding laterally when subjected to a tensile stress. Performances of these materials such as a negative Poisson’s ratio always have increased shear stiffness, synclastic curvature (dome shaped), fracture toughness, and indentation resistance, especially for excellent energy absorption and damping properties what is suitable for their potential applications in the manufacture of advanced protective clothing (e.g. body armour, helmet, etc.), shape adaptive materials, and smart textiles.
Poisson’s ratio is a physical parameter, it is independent of the material scales, and auxetic behavior can be achieved from the molecular to macroscopic scale.
Preparation of auxetic fibers (yarn, fabric, composite) by creating auxetic geometries including helical, rope-like, honeycomb, and porous polymer-like structures or by combining with 3D printing, thermomechanical treatment, and chemical modification technologies are of great attention.
Construction steps of Auxetic materials
1. step:
HAY geometric structure is constructed by incorporating of two different components on a hollow-spindle covering system, as shown in Figure 1(a), and the geometric parameters of the HAY under different strain levels are defined in Figure 1(b) and (c). D and d defined the initial diameters of the core and wrap yarns.
Fig. 2.9.2. Preparation of auxetic fibers/yarns
2 step:
Fabrication of elastic woven fabrics based on HAYs
Weaving or knitting conventional yarns in an auxetic geometrical architecture and fabricating woven fabric through auxetic yarn directly are two main methods to create fabrics with auxetic behavior. Investigation of the auxetic behavior of fabrics, woven fabrics with different patterns is fabricated: plain weave and basket weave (2/2) were chosen to evaluate the effect of the structure on the auxetic properties of the fabric, a derivative weave with the warp and weft yarns arranged in a series of zigzag was designed also and showed at figures a, b, c) illustrated the 3D structure.
Figure 2.9.3. 3D structure design schematic: (a) plain weave; (b) basket weave; and (c) derivative weave.
3. step:
Measurement methods of properties of elastic woven fabrics could be realised using Tenstile test and Auxetic behavior test:
- Tensile test
The elastic woven fabrics were mechanically characterized for tension with reference to standard ASTM D3107-1975 and BS 4592-1992 on Tensile tester.
- Auxetic behavior test
To evaluate the NPR behavior of the as-fabricated fabric samples, firstly, a high-resolution camera (SONY A7R3) was placed on a tripod in front of the fabric tensile system. Five tests were carried out for each image in order to ensure higher accuracy of the NPR. The results were summarized and converted to NPR values based on equation (1). A square with a side length of 10mm was drawn in themiddle of each sample tomeasure the dimension change of the square, as shown in Figure (right)
Fig. 2.9.4. Schematic representation of auxetic material and testing of sample using tensile system
Source: Textile Research Journal 2020, Vol. 90(7–8) 809–823 DOI: 10.1177/0040517519881814
Auxetic materials can be used in composite materials to promote fiber reinforcement in textiles for crash helmets and sports clothing, as sponges, as ropes, in filtration and as shock absorbing materials.
They have a lot of
potential applications, from biomedical to automotive and
defense industries. Also, these materials could potentially
be used for completely new structures with special functions.
Generally, two approaches to producing auxetic textiles: the first one includes the use of auxetic fibers to produce an auxetic textile structure, whereas the other utilizes conventional fibers to produce an auxetic textile structure.
- Auxetic Polymers
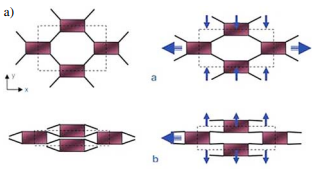
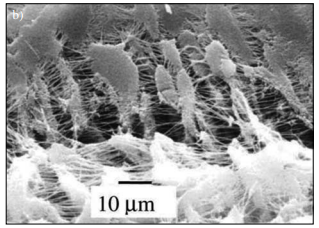
Fig. 2.9.5. left) Schematic representation of auxetic effect – fibrils act as hinges to cause the nodules to translate (a – conventional structure, b – auxetic structure) - left side, and Microstructure of expanded PTFE - right side (source: K. L. Alderson, Actual. Chim., 2012, 360, 73–77.).
Alderson and Evans presented a similar microstructure of a microporous form of ultra high molecular weight polyethylene (UHMWPE) produced by a novel thermoforming processing route. These polymers demonstrate Poisson’s ratios as low as –1.2, depending on the degree of anisotropy in the material.
A similar three-stage thermal processing route was used to engineer polypropylene and nylon also consisting of nodules interconnected by fibrils.
At the other hand, we have the polymers were produced with finely divided powder with a rough surface, by sintering and extruding the powder through a conical die. Powder morphology - particle shape, size, and surface roughness are critical variables for successful processing the auxetic behavior. The negative Poisson’s ratio values for such polypropylene polymers were up to –0.22 at 1.6% strain.
- Auxetic Fibers
Alderson et al. were the first to successfully produce auxetic fibers. They developed a kind of auxetic polypropylene (PP) fiber by employing a novel thermal processing technique, based on modified conventional melt spinning technique. This enabled a continuous fabrication process of auxetic polypropylene (PP) fibers. They used a laboratory scale melt extruder in place of a benchtop extruder and a flat profile of 159 °C across all zones of the extruder (source: K. L. Alderson, Actual. Chim., 2012, 360, 73–77).
Main approach: Production of auxetic fibers lies in maintaining the minimum draw ratio reported Ravirala (Phys. Stat. Sol. (b), 2005, 242, 653–664).
Partial melt extrusion technique could be used to produce auxetic fibers from polyester and nylon. Key processing parameter was extrusion temperature which played a critical role
in attaining the auxetic effect. Auxetic behavior of polyester fibers increased in the fibers processed at
a temperature of 225 °C, in comparison to fibers fabricated at 220 °C - the auxetic effect occurs over an extremely narrow temperature window. Such approch were applied to polypropylene and nylon fibers. This thermal processing technique result in lower modulus fibers which cannot be drawn to improve mechanical properties, but heat treatment improved the properties (strength) just enough to allow textile production, while limiting its overall effect. The reason for this kind of behaviour lies in the microstructure of the fibers.
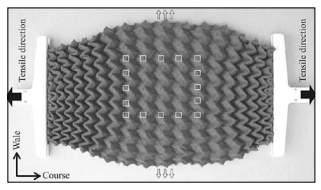
Fig. 2.9.6. Foldable weft knitted auxetic structure (source: Textile Res. J., 2010, 80, 856–863.)
Source: Auxetic Textiles, Acta Chim. Slov. 2013, 60, 715–723, Auxetictextiles-review_ACSI-4-2013.pdf
Examples of AUXETIC materials
👉 Useful link: Appl. Sci. 2018, 8(6), 941; https://doi.org/10.3390/app8060941
👉 Useful video:
👉 Useful video;