TEACHING MATERIALS for Students
2. New technologies for textile functionalization
2.4. Microencapsulation process
Microencapsulation - general
A wide range of functional finishing of fabrics can be obtained by using a microencapsulation technique , which is widely used in the pharmaceutical industries and belong nanotechnology but here will be presented and explained as separate subchapter.
Beside a quite number of PCMs, for textile applications is limited on few of them, since the PCMs in textiles are required to have suitable temperature range, high latent heat capacity, a stable chemical property and be non-toxic and comfortable. According to the mentioned requirements, paraffin was found to be one of the most promising PCMs for textiles. To avoid the leakage of PCMs while transferring to the liquid state, encapsulation of PCMs was developed and has become the most effective method.
This technology enables to carry out several liquid or solid agents (fragrant, flame-retardant agents, antibacterial, etc.) that are encapsulated in phase-changing materials acting as binders (e.g. wax) and can be used to develop odor-eliminating finishes of fabrics, as well as fire-retardant and anti-microbial agents that can also be microencapsulated for advanced fabric finishing.
Fig. 2,4,1, Classification of phase change materials (PCMs)
Substances for microencapsulation
- PCM (Phase change materials) definition (usuful link: https://en.wikipedia.org/wiki/Phase-change_material)
Phase change materials (PCMs) are capable of absorbing or releasing a large amount of energy in the form of latent heat at a narrow temperature range during phase transitions, which could be solid–solid, solid–liquid,solid–gas, liquid–gas or vice versa. PCMs with solid–liquid phase transition are most widely used due to their high heat storage capacity, limited volume change and wide range of temperature adjustment.
Fig. 2.4.2.
Core materials: PCM microcapsules are made from paraffin, organic non-paraffins (fatty acids), salt hydrates, low melting point metals and alloys, or commercial PCMs,
Shell materials: Polymethyl methacrylate (PMMA), polystyrene or polyurethane, etc.
Microencapsulation techniques can be classified into three major categories for functional textiles:- chemical processes (interfacial polymerization, in-situ polymerization, photopolymerization),
- physico-chemical processes (simple and complex coacervation and molecular inclusion),
- physical processes (spray drying, solvent evaporation).
Application of PCMs for:
- thermo-recycling systems,
- energy saving building materials,
- smart materials,
- astronaut suits against the extreme temperature fluctuations in outer space,
- thermoregulating textiles.
Methods of application of PCM microcapsules
A) During the fiber spinning - wet and dry process from solution, melt, electrospinning.
- spinning microemulsion was extruded from a commercial spinneret by providing 0.5 MPa nitrogen gas, which controlled by a pressure regulator,
- spinneret contained 50 holes, each diameter of 70 μm.,
- extruded microemulsion went through a 4% CaCl2 coagulation solution at a temperature of 35ºC for 3 minutes,
- spun alginate fibers had a draft ratio of 1.5, and were dried at room temperature.
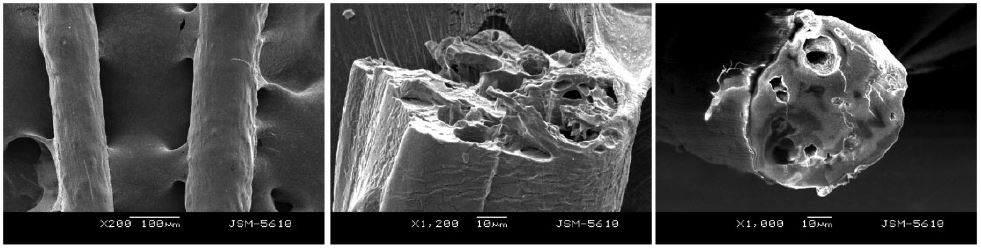
- SEM morphology of calcium alginate fiber containing spherical PCM microemulsion size of around 3 μm, well dispersed in the emulsion, smooth surface of alginate fiber, figure.
- Thermo-regulation alginate fiber had a comfortable phase change temperature of 25–35 ºC, and an acceptable phase change enthalpy of about 20 J/g.
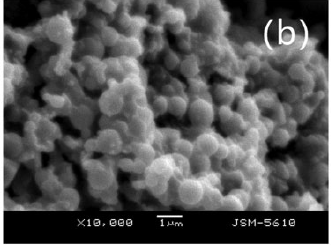
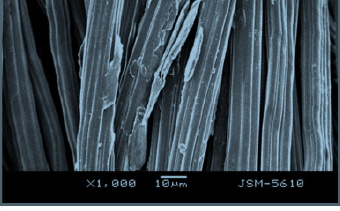
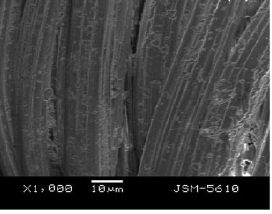
Lamination process of PCMs
For improving the thermo-physiological wearing comfort of protective garments, PCM are incorporated into a thin polymer film and applied to the inner side of the fabric system by lamination process.
Beside chemical protective suits the PCM can also improve the thermo-physiological wearing comfort of other protective garments made of nonwovens such as surgical gowns, uniforms, or garments worn in clean rooms. Microcapsules would be mixed into a water-blown polyurethane foam mix and these foams are applied to a fabric in a lamination process, where the water is taken out of the system by drying process. The excellent honeycomb structure obtained during foam formation made considerable amount of still air trapping possibility, thus, leading to an increased passive insulation.
2. Different essential oils, vitamins, hydrating agents, antibiotics, disinfectants, dyes and pigments, etc.
Microencapsulation using different ingredients as core material offers many opportunities to improve properties or provide entirely new functionalities of textile materials, see in figure 2.4.7. below.
Fig. 2.4.7. Microencapsulation in functional textiles using different ingredients as core material
Source: Coatings 2021, 11, 1371. https://doi.org/10.3390/coatings11111371
Effects of Microencapsulation in Functional Textiles
- Permanent protection or separation of a core material for the life of the product. Such long-life microcapsules provide permanent functionalproperties of active thermal regulation or colour-changing textiles with electrochromic, photochromic and thermochromic materials (using PCMs).
- Targeted release of the core - targeted release of active components from the core is envisaged, microcapsules with impermeable shells burst open by mechanical pressure, abrasion, melting or thermal decomposition. Until release, the active components in the microcapsule core remain separated from the reactive components (leuco dyes and colour developers), converted from a liquid to a solid state and protected against evaporation (essential oils) or protected against environmental influences and oxidation (essential oils, lipids and vitamins).
- Long-lasting, gradual release by diffusion through the permeable microcapsule shell - principle is used in long-lasting perfumed textiles, in insect repellent fabrics and in sustained-release medical and cosmetic textiles.
Note: In the chapter 3. Functional properties read more about properties obtained with microcapsules.
References:
Erkan, G., and Sariisik, M., Colourage, 51, 61 (2004)
Buschmann, H. J., and Schollmeyer, E., Mell. Textil., 84, 84 880 (2003)
Ahmed Hassan et al.: Sustainability 2016, 8, 1046; doi:10.3390/su8101046
Yan Wang et al.: Textile Research Journal, 2020, Vol. 90 (9–10) 1038–1044
Guoqing Zhang et al.: Textile Research Journal 2019, Vol. 89 (16) 3387–3393
Bojana Boh Podgornik et al.: Coatings 2021, 11, 1371. https://doi.org/10.3390/coatings11111371
For all which want to learn more about microencapsulation, please open usuful link and follow video presentation.Usefull link: Textile Research Journal 2019, Vol. 89(18) 3860–3870, sagepub.com/journals-permissions DOI: 10.1177/0040517518824842, journals.sagepub.com/home/trj