TEACHING MATERIALS for staff trainess
3. Functionalization of textiles using nanotechnology
In this chapter students/lerners will be introduce with functional properties of textiles based on novel technology and biomimetic approach from nature which will be by using appropriate techniqes transfered onto the textiles surface and structure. Learners will be informed how complex textile structure influenced on the treatment effectiveness and desired properties.The requirements for textile materials (and thus protective clothing and footwear) require continuous improvement of the production process of polymers, fibers, materials, clothing, footwear and equipment, which take on new properties and thus provide the necessary protective properties, such as:
- heat protection,
- flame protection,
- chemical protection,
- UV radiation,
- various radiation sources (ionized),
- reduction of tendency to static electricity (antistatic properties),
- anti-ballistic properties,
- mechanical hazards,
- resistance to microorganisms (bacteria, viruses),
- water repellent properties,
- waterproofing,
- and combinations of protective
properties.
It is well known that natural fibers like cotton which is a widely used fiber exhibits high absorbency, softness, and breathability, but relatively low strength, low durability, easy creasing and soiling, and flammability. Opposite of that, synthetic fibers can be antimicrobial and stain/crease-resistant but generally lack comfort as compared to cotton. The development of new fiber types that combine the advantages of both natural and synthetic fibers, as well as offering novel functions, has been desirable since the 1940s.
Customer demand for improved appearance color, shape, texture, aesthetic properties, and functionality has also increased. The applications of the functionalized textiles include medical monitoring of body function and metabolism, rehabilitation and electronic devices integrated into clothes. Furthermore, these technologies allow integrating sensors, flexible electronics and optical devices into textiles.
A new frontier in clothing technology is nanoengineered functional textiles.
The advantage of nanomaterials concerns creating function without altering of their comfort properties. Integrated materials and technologies offer a platform that responds to mechanical, chemical, electrical, thermal, optical, or magnetic stimuli. Such wearable devices may include sensors, data transmission, and processing units. These engineered materials should seamlessly integrate into garments and be flexible and comfortable while having no allergic reaction to the body.
A significant challenge in the textile industry is that conventional approaches to functionalize fabrics do not lead to permanent effects. For example, laundering decreases imparted functional effects. Hence, nanotechnology can play a part in introducing new and permanent functions to fabrics.
Textiles can be nanoengineered to have specific functions including hydrophobicity, conductivity, antibacterial properties, antiwrinkle properties, antistatic, and light guidance and scattering (Figure below). Using nanotechnology, these properties can be achieved without affecting breathability or texture of textiles.
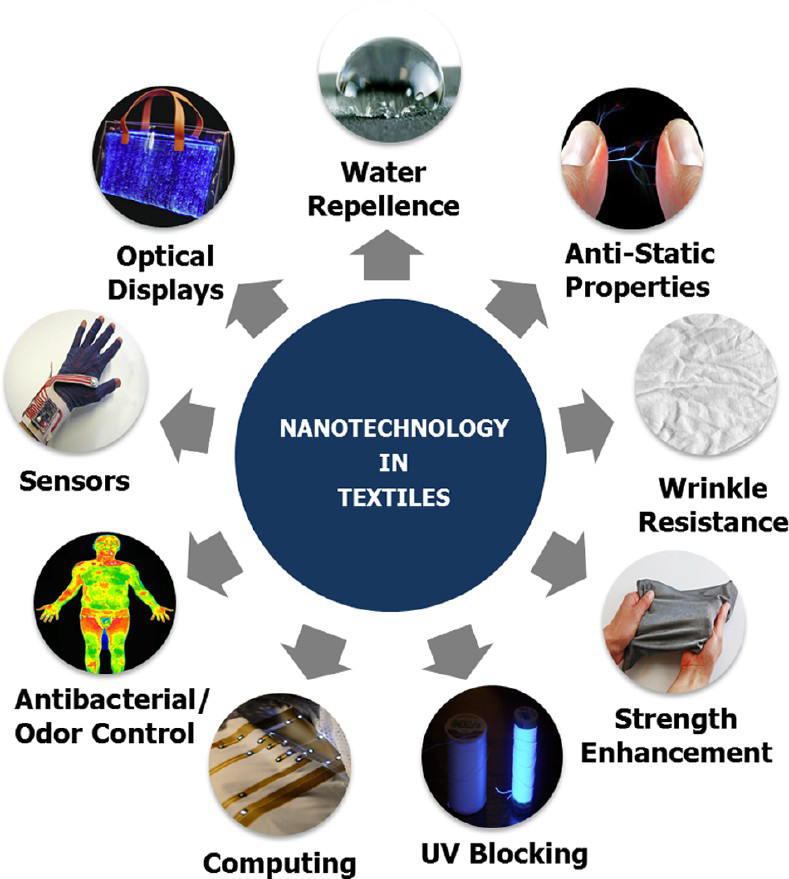
Applications of nanotechnology in textiles
The manufacturing of functional textiles can be classified into two groups:
2. The other is to modify the textile surfaces by functional biomaterials, resins, finishes.
- NANOENGINEERED TEXTILES
Water and Oil Repellence by forming Nano Whiskers - keep the fabric breathable. Nanowhiskers consisting of hydrocarbons that are 3 orders of magnitude smaller than a typical cotton fiber. Nanowhiskers are integrated within the fabric to create a peach fuzz effect. The spaces between individual whiskers are smaller than a drop of water but larger than water molecules, producing a high surface tension that allows the water to remain on the surface (like Lotus effect).
Fabric posses: Water and oil repellency, Superior durability, Fabric remains soft, natural wrinkle resistance.
Water repellence can also be induced through creation of 3D surface structures on the fabric by adding gel forming additives or coating the textile with nanoparticulate film.
In that case, the audio frequency (AC) plasma of fluorocarbon chemical was applied to deposit a nanoparticulate hydrophobic film onto a cotton fabric surface. The measurement of the contact angle showed that the superhydrophobicity of the cotton fabric was obtained with a treatment of only 30 s. Hydrophobic cotton fabric coated by a thin nanoparticulate plasma film and producing roughness on the surface of the fabric, superhydrophobicity can be created without affecting abrasion resistance and softness of the fabric.
Also, SiO2 nanoparticles (NPs) with water-repellent agents can ensure hydrophobicity to textiles. SiO2NPs (143−378 nm) were synthesized via a sol−gel process, and cotton fabrics after treatment with both of them have contact angles above 130°.
Hydrophobicity can be ensured with SiO2 which cotton surface make more roughness while the perfluorooctylated quaternary ammonium silane coupling agent (PQASCA) decrease surface energy, and resulted in water repellence with a water contact angle of 145°. Oil repellency of the fabric also improved, showing a 131° contact angle for a diiodomethane (CH2I2) droplet on the fabric surface.
Treatments organic–inorganic hybrid micro-nanoparticles
Silica dioxide nanoparticles (SiO2) were synthesized and functionalized with n-octadecyltriethoxysilane (OD) through a modified Stöber method for the preparation of organic–inorganic hybrid micro-nanoparticles - applied onto the polyester (PET) fabric via a conventional “dipping–drying” process for the fluoro-free water-repellent textile materials.
Mechanism:
The coated PET fabric surface showed micro/nano-structures and exhibited hydrophobic behavior with water contact angle of 141°. PET hydrophobic fabrics exhibited excellent self-cleaning properties with dyes on the fabric surface (see figures below):
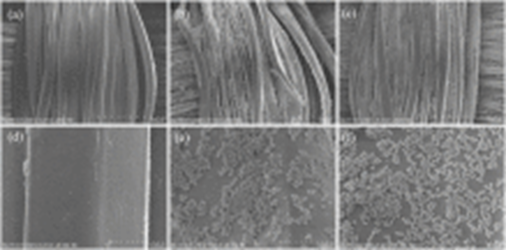
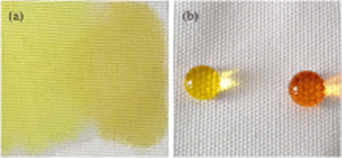
Source: https://doi.org/10.1016/j.jiec.2019.12.016
Antibacterial
textiles
- Ag, TiO2, and ZnO NPs are most common agents to impart antibacterial and fungicidal properties to textiles.
The antiseptic mechanism of Ag NPs is based on reacting with proteins in these organisms and adversely affecting their cellular function and inhibiting cell growth. They also reduce respiration, limiting the activity of the basal metabolism of the electron transfer system, and substrate transport into the cell membrane. When Ag NPs contact with moisture or bacteria, they adhere to the cell wall and membrane
The Ag+ ions are reactive (Ag NPs in their metallic state are inert, and they need to be ionized in the presence of moisture) and they diffuse through the cell wall and membrane into the cytoplasm. Ag+ ions bind to sulfur-containing proteins on the cell membrane to structurally change the cell wall. These structural changes result in the release of the cellular components to extracellular fluid due to the changes in the osmotic pressure. Additionally, the Ag+ ions bind to phosphate containing proteins to condense DNA, leading to a reaction with thiol group proteins to cause cell death. They also suppress the function of enzymes and inhibit the cell to produce ATP.
Source: ACS Nano 2016, 10, 3042−3068 DOI: 10.1021/acsnano.5b08176 ACS Nano 2016, 10, 3042−3068
CASE STUDIES (from: https://doi.org/10.1021/acsnano.5b08176)
"NanoSphere marketed by Schoeller Textiles AG (Sevelen, Switzerland) is a finishing technology with hydrophobic surface properties that mimic the self-cleaning effect of lotus leaves. Schoeller claims that NanoSphere has improved water/oil- and dirt-repelling properties and washing performance compared to traditional textile impregnation-based manufacturing. Furthermore, the protective function of NanoSphere may be retained after frequent use and numerous washing cycles without affecting comfort, texture, and breathability. The textiles finished with NanoSphere require less frequent washing at lower temperatures as compared to conventional textiles. Additionally, it has high abrasion resistance. The company’s other products address a variety of applications ranging from stretch fabrics, sun reflectors, temperature resistance, and bionic climate conditioning. Their patent portfolio in nanotechnology includes PEIN NPs for antibacterial finishing of electrospinnable polymers, NPs and CNTs for finishing of substrates, and nanofibers having microbicidal properties."
"Aquapel marketed by Nanotex LLC (Bloomfield Hills, MI), reproduces natural water repellency of plant surfaces and animal coats. Aquapel technology involves permanent attachment of hydrophobic “whiskers” to individual fibers at the molecular level. Aquapel features a hydrocarbon polymer that is ecologically friendly and low cost. Nanotex’s portfolio consists of 28 WO patent applications and addresses textile sectors including repellency/stain resistance, moisture management, odor control, static elimination, and wrinkle resistance. In 2013, Nanotex products were at $280 million in branded products at retail. In the same year, Nanotex was acquired by soft-surface technology company Crypton Inc."
"SmartSilver is an antimicrobial yarn marketed by Nano-Horizons (Bellefonte, PA). It develops and manufactures Ag NP additives that provide antimicrobial characteristics to their products. The company markets Oeko-Tex antimicrobial solution under the SmartSilver brand."
"Nanosan, marketed by SNS-Nano Fiber Technology (Hudson, OH) and Schill & Seilacher (Germany), consists of spun polymers for application in filters and adsorbent fabrics. SNS-Nano Fiber Technology integrates microscale particles into the nanofiber structure at high-volume production. Nanosan fibers can be engineered to function as high-strength, absorbent, or flexible material. Its product line consists of nanofiber matrixes with different absorption properties. The applications of Nanosan include filters, medical and military products, and personal care products such as cosmetics. Its patent portfolio includes debris and particle-absorbent materials. The company is currently exploring the use of nanofibers for skin decontamination."
"Wearable Motherboard (electronic shirt), marketed by Sarvint Technologies, Inc. (Atlanta, GA), uses engineered fibers to sense body signs, such as heart rate, temperature, skin conductivity, muscle exertion, blood pressure, and respiration rate. Its patent portfolio includes the use of engineered fabric-based sensors (e.g., conductive fibers) for monitoring vital signs. Its technology comprises microporous elastic Spandex fiber, a polyester−polyurethane copolymer invented in 1958. Table 1 shows the companies involved in smart textiles and wearables market. Some of these companies use microtechnology as opposed to nanotechnology in apparel."
Examples of functional material:
Three Dimensional Molecular Nano Net completely cover the core fiber.
Alters the property of synthetic fibers - Polyester to give a feel of cotton & linen, much better wicking properties, quickly drying gives the cooling effect.
Nano sheet wraps the fiber completely to cover it & alter its property.
Incresed Strength and Durability, Improvement in colorfastness and Crease Retention as well as Static Resist.