TEACHING MATERIALS for researchers/teachers trainees
Site: | ICT-TEX platform |
Course: | Novel trend in textile functionalization |
Book: | TEACHING MATERIALS for researchers/teachers trainees |
Printed by: | Guest user |
Date: | Thursday, 21 August 2025, 11:53 AM |
Description
1. Introduction
In this course students/ learners will be introducing with novel trends in textile functionalization through:
- new technologies,
- methods,
- processes and
- functional properties of such treated textiles.
Functional materials - a special category of materials in which the application of targeted chemical, mechanical treatments/ finishing has achieved some new properties in the function of protection.
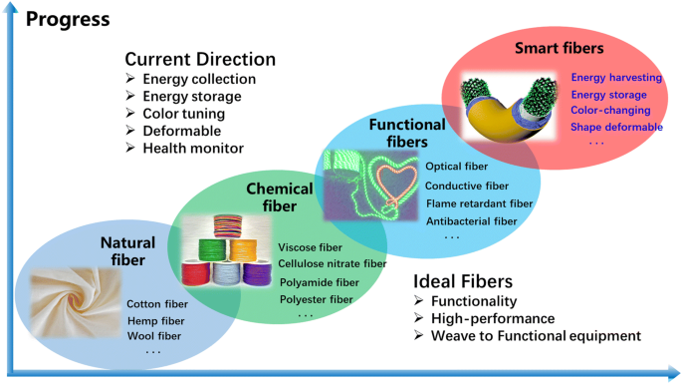
Some of established techniques which could be used to impart new functionalities and properties to textile materials including:
- plasma processing,
- electrospinning,
- sol-gel process,
- nanotechnology,
- wet processes,
- spraying,
- polymer coating,
- layer by layer,
- biotechnological treatment.
The requirements for textile materials (and thus protective clothing and footwear) require continuous improvement of the production process of polymers, fibers, materials, clothing, footwear and equipment, which take on new properties and thus provide the necessary protective properties, such as:
- heat protection,
- flame protection,
- chemical protection,
- UV radiation,
- various radiation sources (ionized),
- reduction of tendency to static electricity (antistatic properties),
- anti-ballistic properties,
- mechanical hazards,
- resistance to microorganisms (bacteria, viruses),
- water repellent properties,
- waterproofing, and other protective properties.
2. New technologies for textile functionalization
Through the application of a new technologies as an emerging tool for improving textile performance and increase its added value, learners will be learned about specific functional properties of textiles as self-cleaning,
super-hydrophobic, antimicrobial, flame retardant, etc. which are results of
functionalization of textiles using such innovative tecnologies.
Direction of development of functional textiles
Analysis of Research Fronts in Scientific Publications on “Functional Textiles” 1989–2012 (Depicted are 8931 recorded articles). Arrows indicate the dynamic of research activity over the last years: green arrows indicate that a topic is increasing, red arrows that a topic is decreasing or stable. The graph was drawn up by AIT using BibTechMon™.
2.1. Plasma technology
Due to the increasingly stringent environmental requirements set in modern textile technology processes, increasing importance is attached to treatment by agents that are acceptable from an environmental point of view. In this sense, there has been more research related to the use of plasma as an environmentally friendly physical agent. Although known from before, a special interest in the application of plasma technology in the field of textiles has been recorded in the last ten years, especially in the processes of pre-treatment and finishing of textile materials for the purpose of obtaining multifunctional textile products. In this sense, the emphasis of modern treatment is focused on obtaining favorable effects by modifications of the fiber surface (textiles), which ultimately contribute to the overall quality of the textile material. Surface treatments with plasma, ozone, biopolymers, etc. which are being researched and implemented nowadays for the purpose of modifying the properties of textile materials, are, in addition to being environmentally friendly, also more energy efficient compared to conventional finishing methods. The development and commercialization of plasma technology in the design and production of modern textile materials contributes to reducing the use of chemical agents, which is gaining increasing importance - both from an environmental and economic point of view.
Plasma shapes and types are numerous and plasmas can be classified according to several criteria. Plasmas occurring in nature differ primarily in density (an order of magnitude of more than 10 exponents), and accordingly the differences in physical properties are extreme as well. A key parameter for distinguishing technical plasmas is the pressure of the neutral gas in which the ionized particles move relative to atmospheric pressure. According to this criterion, plasmas are classified into low-pressure, high-pressure and atmospheric pressure plasmas (atmospheric plasmas).
According to the temperature at which they are applied, plasmas are divided into cold and hot plasmas. Low-pressure plasma is an example of cold or low-temperature plasma, which is also an example of non-equilibrium plasma, which means that electrons in plasma have a much higher temperature than the temperature of heavier ion particles in plasma. With appropriate external gas excitation in such a plasma, it is possible to achieve conditions in which the gas temperature is close to room temperature, while the effective temperature and kinetic energy of the electron are much higher and large enough to maintain plasma and initiate plasma-chemical reactions. The temperature of the electrons Te is of the order of magnitude 104 to 105K, while the temperature of heavy particles of ions and other particles of molecules, atoms and free radicals is close to room temperature, so that the gas hardly heats up and maintains room temperature. Therefore, such plasma is particularly suitable for the treatment of thermally sensitive materials such as most textile materials.
In equilibrium plasmas there is a thermal equilibrium, i.e. the temperature of electrons and heavier ion particles is equal and usually high, and the kinetic energy of all particles is high. In a surface treatment application, such plasmas would be significantly more efficient in the production of radicals and the flow of ions coming to the surface of the material. However, since they develop a high temperature due to the high degree of ionization, it is very difficult to control the energy of particles and thus optimize the production conditions of specific radicals, and it is impossible to process thermally unstable materials. Such hot plasma is not suitable for textile applications, but is used in welding, thermal spraying, metal cutting and as a method for determining metals in water analysis.Cold plasma, both low-pressure plasma and atmospheric plasma, are suitable for textile applications. Low-pressure plasmas are obtained in a diluted gas whose pressure is significantly lower than atmospheric pressure, while atmospheric plasma is produced at normal atmospheric pressure. Therefore, a vacuum chamber or a vacuum pump is not required to obtain atmospheric plasma, while such equipment is necessary in the production of low-pressure plasma.
Plasma action mechanism
Plasma affects the surface of the substrate chemically and physically, with the reactions between the plasma and the surface depending on the type of gas used and its chemical properties. Textile materials subjected to such treatments undergo chemical and physical transformations related to chemical changes in the surface layer, changes in the structure of the surface layer and changes in the physical properties of the surface layer. Plasma creates a high density of free radicals during the dissociation of molecules during electron collisions and photochemical processes. This causes the destruction of chemical bonds in the polymer surface of the fiber resulting in the formation of new chemical entities. The action of plasma on the surface of fibers and polymers results in the creation of new functional groups such as –OH, –C=O, –COOH, which affect the improvement of the wettability of fabrics (hydrophilic effect), and can be active centers for graft polymerization of different molecules.
Therefore, plasma is primarily used for surface treatment of materials, because its action modifies only the surface properties to a layer thickness of only a few tens of nanometers, leaving the basic properties of the material almost unchanged. In this way, selective modification of fiber properties is achieved, e.g. it can affect the ability to wet and dye, adhesion characteristics, etc., which can hardly be achieved by classical chemical processes without affecting the basic properties of such processed fibers. In general, the action of plasma on the surface of a textile material can be roughly described through four groups of processes, Figure 1:
- Plasma cleaning of the surface,
- Plasma ablation or etching of the surface,
- Surface activation, plasma modification,
- Deposition, plasma polymerization.
Figure 1. Schematically shows these four types of actions and their effects in comparison with the untreated surface of the material.
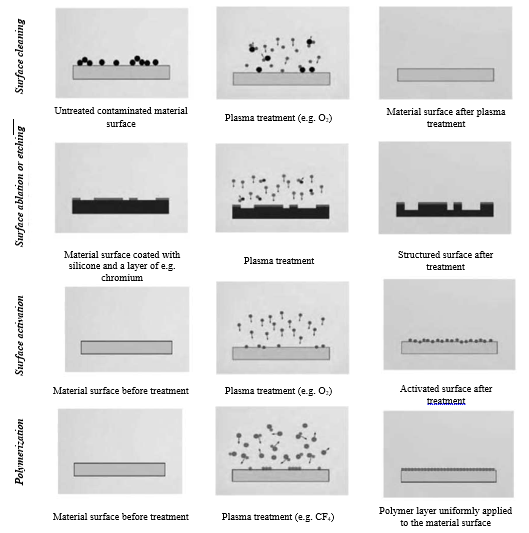
Figure 1 Schematic diagram of plasma action on substrate surface
Source:
S. ERCEGOVIĆ RAZIĆ, R. ČUNKO: Modification of textile properties using plasma, Textile 58 (3) 55-74 (2009), A Review https://platform.ict-tex.eu/pluginfile.php/4110/mod_book/chapter/77/Textile_2009_Review.pdf
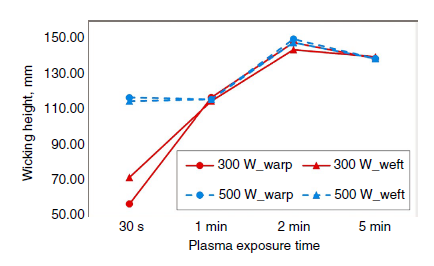
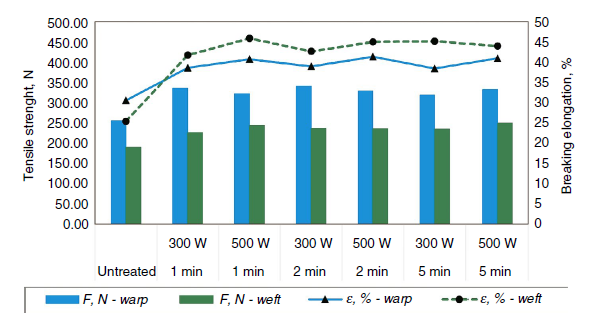
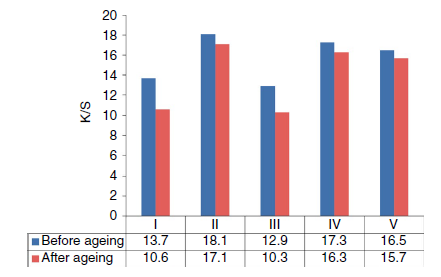
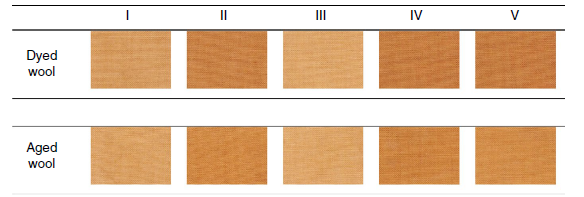
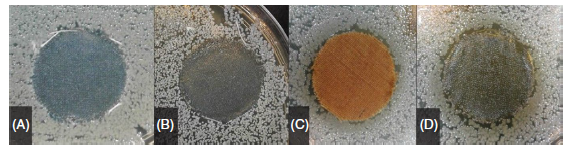
2.2. Electrospinning technology
Electrospinning is a method based on the use of electrostatic forces for producing continuous fibres with the diameter from between ten nanometres to a few micrometres (https://en.wikipedia.org/wiki/Electrospinning#cite_note-reinventing_the_wheel-5). Such fine fibres cannot be produced with conventional methods for the production of nonwovens. The nanofibres formed with electrospinning have an exceptionally large active surface area per mass unit (fibre surface at diameter of 100 nm equals 40 m2 /g) and the spinning process itself enables a planned formation of the web structure (e.g. planned size of pores in the web by adjusting the nanofibre diameter and fibre thickness). Nanofibres can be electrospun from synthetic or natural polymers and their blends, from polymers with various nanoparticles (metal or ceramic), active substances etc. Also, individual fibres can be fabricated, as well as webs with a random or planned fibre arrangement. Fibres with a complex structure, e.g. core shell or hollow fibres, can be produced with a special electrospinning method. Regarding the advantages demonstrated by the nanofibres fabricated with electrospinning, this procedure has become an important part of research in several fields of use of technical textiles, e.g. shielding materials, air and oil filters in the car industry, agrotextiles and most of all medical textiles. The method can also be used in the production of batteries and photovoltaic cells.
Electrospinning shares characteristics of both electrospraying and conventional solution dry spinning of fibers. The process does not require the use of coagulation chemistry or high temperatures to produce solid threads from solution.
When a sufficiently high voltage is applied to a liquid droplet, the body of the liquid becomes charged, and electrostatic repulsion counteracts the surafce tension and the droplet is stretched; at a critical point a stream of liquid erupts from the surface. This point of eruption is known as the Taylor cone. If the molecular cohesion of the liquid is sufficiently high, stream breakup does not occur (if it does, droplets are electrosprayed) and a charged liquid jet is formed.
As the jet dries in flight, the mode of current flow changes from ohmic to convective as the charge migrates to the surface of the fiber. The jet is then elongated by a whipping process caused by electrostatic repulsion initiated at small bends in the fiber, until it is finally deposited on the grounded collector.[4] The elongation and thinning of the fiber resulting from this bending instability leads to the formation of uniform fibers with nanometer-scale diameters.[5]
Diagram showing fibre formation by electrospinning
Parameters for electrospinning process:
- Molecular weight, molecular-weight distribution and architecture (branched, linear etc.) of the polymer
- Solution properties (viscosity, conductivity and surface tension)
- Electric potential, flow rate and concentration
- Distance between the capillary and collection screen
- Environmental parameters (temperature, humidity and air velocity in the chamber)
- Motion and size of target screen (collector)
- Needle gauge
Modification of the spinneret and/or the type of solution can allow for the creation of fibers with unique structures and properties. Electrospun fibers can adopt a porous or core–shell morphology depending on the type of materials being spun as well as the evaporation rates and miscibility for the solvents involved. For techniques which involve multiple spinning fluids, the general criteria for the creation of fibers depends upon the spinnability of the outer solution.[5] This opens up the possibility of creating composite fibers which can function as drug delivery systems or possess the ability to self-heal upon failure.[26][27]
Co-axial electrospinning
A coaxial setup uses a dual-solution feed system which allows for the injection of one solution into another at the tip of the spinnerets. The sheath fluid is believed to act as a carrier which draws in the inner fluid at the Taylor Cone of the electrospinning jet.[5] If the solutions are immiscible then a core shell structure is usually observed. Miscible solutions however can result in porosity or a fiber with distinct phases due to phase separation during solidification of the fiber. For more advanced setups, a triaxial or quadaxial (tetra-axial) spinneret can be used with multiple solutions.
Emulsion electrospinning
Emulsions can be used to create core shell or composite fibers without modification of the spinneret. However, these fibers are typically more difficult to produce compared to coaxial spinning due to the greater number of variables which must be accounted for in creating the emulsion. A water phase and an immiscible solvent phase are mixed in the presence of an emulsifying agent to form the emulsion. Any agent which stabilizes the interface between the immiscible phases can be used. Surfactants such as sodium dodecyl sulfate, Triton and nanoparticles have been used successfully. During the electrospinning process the emulsion droplets within the fluid are stretched and gradually confined leading to their coalescence. If the volume fraction of inner fluid is sufficiently high, a continuous inner core can be formed.[29]
Electrospinning of blends is a variation of this technique which uses the fact that polymers are generally immiscible with each and can phase segregate without the use of surfactants. This method can be simplified further if a solvent which dissolves both polymers is used.[30]
Melt electrospinning
Electrospinning of polymer melts eliminates the need for volatile solvents in solution electrospinning.[31] Semi crystalline polymer fibers such as PE, PET and PP, which would otherwise be impossible or very difficult to create using solution spinning, can be created. The setup is very similar to that employed in conventional electrospinning and includes the use of a syringe or spinneret, a high voltage supply and the collector. The polymer melt is usually produced by heating from either resistance heating, circulating fluids, air heating or lasers.[32]
Due to the high viscosity of polymer melts, the fiber diameters are usually slightly larger than those obtained from solution electrospinning. The fiber uniformity upon achieving stable flow rates and thermal equilibrium, tends to be very good. The whipping instability which is the predominant stage in which the fiber is stretched for spinning from solutions can be absent from the process due to the low melt conductivity and high viscosity of the melt. The most significant factors which affect the fiber size tend to be the feed rate, the molecular weight of the polymer and the diameter of the spinneret. Fiber sizes ranging from ~250 nm to several hundreds of micrometershave been created thus far with the lower sizes being achieved using low molecular weight polymers.[33]
Examples: Electrospinning process of “NanospiderTM” equipment
Source: Elmarco-Asia_Company-Brochure_202005.pdf (kazelfacorp.com)
2.3. Sol-gel process
The sol-gel process is a chemical synthesis method where an alkoxide network is created by progressive condensation reactions of molecular precursors from a liquid medium.
The sol-gel process to produce hybrid coatings, compared to other methods, has several advantages. This process is often classified as a “green” technology since it uses compounds that do not introduce impurities into the end product (e.g., ceramic processing), is waste-free, excludes the stage of washing, and the processing temperature is generally low, frequently close to room temperature.
The first step to implement a synthesis through the sol-gel method is to select the chemical compounds, known as the precursors (see Figures below) that are combined forming a sol. This term designates a stable suspension of colloidal particles within a liquid. This first step is a typical chemical transformation aiming the formation of a sol of colloidal particles or a solution of oligomers (small polymers). As sol is a fluid, it can be cast in a mold, or be applied on a surface using various shaping techniques, e.g., spraying on a surface, dipping, or spinning through a set of rotating nozzles. As the sol is a relatively stable solution it can be stored for a certain time before further casting, or applied by any of the above referred methods. Spraying and electrodeposition processes emerged recently and could be the major sol-gel coating application methods in the near future.
Sol-gel coatings Precursors used in the synthesis of hybrid materials
To achieve gelation, the chemical transformations of the sol in gel must be allowed to proceed
until a single and interconnected network forms, only limited by the walls of the container and the
mass of the reactive mixture. Another step in sol-gel art is drying, which is a very critical step. In many instances, a dry gel needs further thermal treatment to be densified.
There are two main methods to prepare sol-gel coatings: the inorganic method and the organic one. The first method involves the evolution of networks through the formation of a colloidal suspension (habitually, oxides) and gelation of the sol (colloidal suspension of very small particles that may vary from 1 to 100 nm) to form a network in a continuous liquid phase.
The most commonly used method to prepare sol-gel coatings is the organic one, which normally starts with a solution of monomeric metal or metalloid alkoxide precursors M(OR)n in an alcohol or other low-molecular weight organic solvent. M represents a network-forming element, such as Si, Ti, Zr, Al, Fe, B, etc., and R is typically an alkyl group (CxH2x+1). This later approach has the advantage of obtaining organic-inorganic hybrid materials combining the behavior of the organic component (polymeric) with the stiffness of the inorganic (alkoxide) backbone.
Generally, the sol-gel method used to obtain hybrid materials (organic method) occurs in four stages:
(i) a hydrolysis reaction of the metal alkoxide groups (–OR) are replaced by the hydroxyl groups (–OH);
(ii) condensation and polymerization of monomers to form chains and particles;
(iii) growth of the particles; and
(iv) agglomeration of the polymer structures followed by the formation of networks that extend throughout the liquid medium resulting in a gel.
Indeed, both the hydrolysis and condensation reactions occur at the same time once the hydrolysis reaction has been initiated. Both the hydrolysis and condensation steps produce low molecular weight by-products, such as alcohol and water.
Field of applications of sol-gel coatings, examples of some will be persented in chapter 3.
Source:
Rita B. Figueira et al.: Coatings 2016, 6, 12; doi:10.3390/coatings6010012
Parashar, M. et al.:: J Mater Sci: Mater Electron 31, 3729–3749 (2020)
2.4. Microencapsulation process
Microencapsulation - general
A wide range of functional finishing of fabrics can be obtained by using a microencapsulation technique , which is widely used in the pharmaceutical industries and belong nanotechnology but here will be presented and explained as separate subchapter.
Beside a quite number of PCMs, for textile applications is limited on few of them, since the PCMs in textiles are required to have suitable temperature range, high latent heat capacity, a stable chemical property and be non-toxic and comfortable. According to the mentioned requirements, paraffin was found to be one of the most promising PCMs for textiles. To avoid the leakage of PCMs while transferring to the liquid state, encapsulation of PCMs was developed and has become the most effective method.
This technology enables to carry out several liquid or solid agents (fragrant, flame-retardant agents, antibacterial, etc.) that are encapsulated in phase-changing materials acting as binders (e.g. wax) and can be used to develop odor-eliminating finishes of fabrics, as well as fire-retardant and anti-microbial agents that can also be microencapsulated for advanced fabric finishing.
Fig. 2.4.1. Classification of phase change materials (PCMs)
Substances for microencapsulation
- PCM (Phase change materials) definition (usuful link: https://en.wikipedia.org/wiki/Phase-change_material)
Phase change materials (PCMs) are capable of absorbing or releasing a large amount of energy in the form of latent heat at a narrow temperature range during phase transitions, which could be solid–solid, solid–liquid,solid–gas, liquid–gas or vice versa. PCMs with solid–liquid phase transition are most widely used due to their high heat storage capacity, limited volume change and wide range of temperature adjustment.
Fig. 2.4.2. Schematic of absorbing or releasing a large amount of energy in the form of latent heat at a narrow temperature range during phase transitions
Core materials: PCM microcapsules are made from paraffin, organic non-paraffins (fatty acids), salt hydrates, low melting point metals and alloys, or commercial PCMs,
Shell materials: Polymethyl methacrylate (PMMA), polystyrene or polyurethane, etc.
Microencapsulation techniques can be classified into three major categories for functional textiles:- chemical processes (interfacial polymerization, in-situ polymerization, photopolymerization),
- physico-chemical processes (simple and complex coacervation and molecular inclusion),
- physical processes (spray drying, solvent evaporation).
Application of PCMs for:
- thermo-recycling systems,
- energy saving building materials,
- smart materials,
- astronaut suits against the extreme temperature fluctuations in outer space,
- thermoregulating textiles.
Methods of application of PCM microcapsules
A) During the fiber spinning - wet and dry process from solution, melt, electrospinning.
- spinning microemulsion was extruded from a commercial spinneret by providing 0.5 MPa nitrogen gas, which controlled by a pressure regulator,
- spinneret contained 50 holes, each diameter of 70 μm.,
- extruded microemulsion went through a 4% CaCl2 coagulation solution at a temperature of 35ºC for 3 minutes,
- spun alginate fibers had a draft ratio of 1.5, and were dried at room temperature.
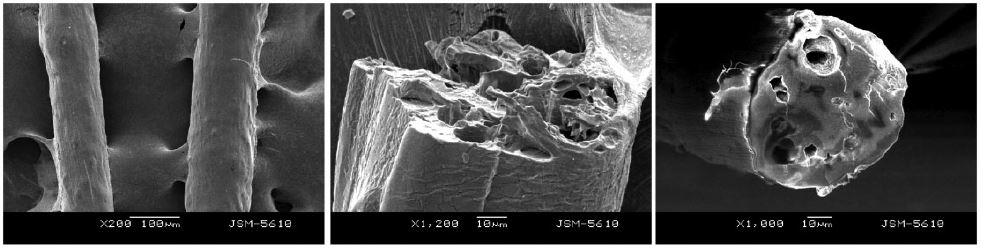
- SEM morphology of calcium alginate fiber containing spherical PCM microemulsion size of around 3 μm, well dispersed in the emulsion, smooth surface of alginate fiber, figure.
- Thermo-regulation alginate fiber had a comfortable phase change temperature of 25–35 ºC, and an acceptable phase change enthalpy of about 20 J/g.
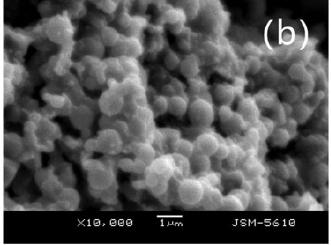
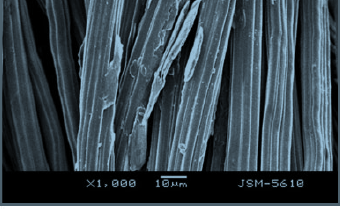
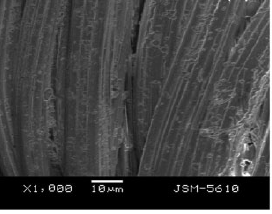
Lamination process of PCMs
For improving the thermo-physiological wearing comfort of protective garments, PCM are incorporated into a thin polymer film and applied to the inner side of the fabric system by lamination process.
Beside chemical protective suits the PCM can also improve the thermo-physiological wearing comfort of other protective garments made of nonwovens such as surgical gowns, uniforms, or garments worn in clean rooms. Microcapsules would be mixed into a water-blown polyurethane foam mix and these foams are applied to a fabric in a lamination process, where the water is taken out of the system by drying process. The excellent honeycomb structure obtained during foam formation made considerable amount of still air trapping possibility, thus, leading to an increased passive insulation.
2. Different essential oils, vitamins, hydrating agents, antibiotics, disinfectants, dyes and pigments, etc.
Microencapsulation using different ingredients as core material offers many opportunities to improve properties or provide entirely new functionalities of textile materials, see in figure 2.4.7. below.
Fig. 2.4.7. Microencapsulation in functional textiles using different ingredients as core material
Source: Coatings 2021, 11, 1371. https://doi.org/10.3390/coatings11111371
Effects of Microencapsulation in Functional Textiles
- Permanent protection or separation of a core material for the life of the product. Such long-life microcapsules provide permanent functionalproperties of active thermal regulation or colour-changing textiles with electrochromic, photochromic and thermochromic materials (using PCMs).
- Targeted release of the core - targeted release of active components from the core is envisaged, microcapsules with impermeable shells burst open by mechanical pressure, abrasion, melting or thermal decomposition. Until release, the active components in the microcapsule core remain separated from the reactive components (leuco dyes and colour developers), converted from a liquid to a solid state and protected against evaporation (essential oils) or protected against environmental influences and oxidation (essential oils, lipids and vitamins).
- Long-lasting, gradual release by diffusion through the permeable microcapsule shell - principle is used in long-lasting perfumed textiles, in insect repellent fabrics and in sustained-release medical and cosmetic textiles.
Note: In the chapter 3. Functional properties read more about properties obtained with microcapsules.
References:
Erkan, G., and Sariisik, M., Colourage, 51, 61 (2004)
Buschmann, H. J., and Schollmeyer, E., Mell. Textil., 84, 84 880 (2003)
Ahmed Hassan et al.: Sustainability 2016, 8, 1046; doi:10.3390/su8101046
Yan Wang et al.: Textile Research Journal, 2020, Vol. 90 (9–10) 1038–1044
Guoqing Zhang et al.: Textile Research Journal 2019, Vol. 89 (16) 3387–3393
Bojana Boh Podgornik et al.: Coatings 2021, 11, 1371. https://doi.org/10.3390/coatings11111371
For all which want to learn more about microencapsulation, please open usuful link and follow video presentation.Usefull link: Textile Research Journal 2019, Vol. 89(18) 3860–3870, sagepub.com/journals-permissions DOI: 10.1177/0040517518824842, journals.sagepub.com/home/trj
2.5. Nanotechnology in textile industry
Nanotechnology (NT) repersents a growing interdisciplinary technology often seen as a new industrial revolution.
NT deals with materials 1 to 100 nm in length. The fundamentals of nanotechnology lie in the fact that the properties of materials drastically change when their dimensions are reduced to nanometer scale.
Nowadays, the textile industry has discovered the possibilities of nanotechnology through understanding, manipulation, and control of matter at the above-stated length, such that the physical, chemical, and biological properties of the materials (individual atoms, molecules, and bulk matter) can be engineered, synthesized, and altered to develop the next generation of improved materials, devices, structures, and systems.
The main goal is - develop desired textile characteristics, such as high tensile strength, unique surface structure, soft hand, durability, water repellency, fire retardancy, antimicrobial properties, and the like.
Nanotechnology offering huge potential in a wide range of end uses and new properties of nano materials have attracted not only scientists and researchers but also businesses, due to their huge economical potential.
Nanotechnology also has real commercial potential for the textile industry;
- it can provide high durability for fabrics, because nano-particles have a large surface area-to-volume ratio and high surface energy, thus presenting better affinity for fabrics and leading to an increase in durability of the function.
- conventional methods used to impart different properties to fabrics often do not lead to permanent effects, and will lose their functions after laundering or wearing. In addition, a coating of nano-particles on fabrics will not affect their breath ability or hand feel.
Below, in the figures you can see the graphical representation of Nanotechnology application on textiles:
Fig. 2.5.1. Textile application of nanotechnology
Fig. 2.5.2. Type of functional textiles based on nanotechnology (left)
Nano whiskers keep the fabric breathable,
Material (fabric) posses: Water and oil repellency, Superior durability, Fabric remains soft, natural Wrinkle resistance.
Three Dimensional Molecular Nano Net completely cover the core fiber.
Alters the property of synthetic fibers - Polyester to give a feel of cotton & linen, much better wicking properties, quickly drying gives the cooling effect.
Nano sheet wraps the fiber completely to cover it & alter its property.
Incresed Strength and Durability, Improvement in colorfastness and Crease Retention as well as Static Resist.
Application of nanotechnology:
- incorporation in fibres and yarns (fabrics),
- textile finishing by coating,
- e-textiles.
Nanoparticles can be introduced in the textile production process at two levels :
- during the melt extrusion of yarns nanoparticles based on clay, metal oxides or carbon nanotubes (CNTs) can be mixed in the polymer before the extrusion process, for obtaining:
- Antibacterial and Deodorant finishes
- Self cleaning clothes
- Water Repellent and Self Cleaning by Nano-Sphere
- during the coating - using padding process and after drying and curing the water compound evaporates; polymer was melted and spread over the surface resulting in uniform coating of fibre due to the nano size of the finishing agent.
A few representative applications of fabric finishing using NT are schematically displayed in figure 2.5.3.
Modification properties with nanoparticles as additive:
By combining the nano-particles of hydroxylapatite, TiO2, ZnO and Fe2O3 with other organic and inorganic substances, the surfaces of the textile fabrics can be appreciably modified to achieve considerably greater abrasion resistance, water repellency, ultraviolet (UV) resistance, and electromagnetic- and infrared-protection properties.
Titanium-dioxide nano-particles have been utilized for UV protection. Similarly, by using nanosized silicon dioxide as an additive in coating materials, significant improvements in the strength and flame-resistance of textile fabrics can be achieved.
Wrinkle resistance can be developed for cotton fabrics by using the nano-engineered cross-linking agents during the fabric finishing process, but also for eliminating toxic agents, while maintaining the desired comfort properties of cotton.
- e-textiles - smart/interactive textiles are materials and structures that sense and react to environmental conditions or stimuli, such as those from mechanical, thermal, chemical, electrical, magnetic or other sources.
Fig. 2.5.4. Warning Signaling - wearable txtiles
The sensors can monitor heart rate, respiration, and temperature. If vital signals were below critical values, a FLED would automatically display, for example, a flashing red light, and a wireless communication system could send a distress signal to a remote location.
Concepts of surface-engineered modifications through NT to develop certain high-performance fabrics, through trademarks:
- superior durability, softness, tear strength, abrasion resistance, and durable-press/ wrinkle-resistance
Nano-Pel technology for stain-resistance and oil-repellency treatments based on the concept of surface engineering and develops hydrophobic fabric surfaces that are capable of repelling liquids and resisting stains, while complementing the other desirable fabric attributes, such as breathability, softness, and comfort.
Nano-whiskers are nano-structures, provide roughness to the fabric surface so that fluid-surface interaction and consequently fluid penetration can be avoided - the treated fabric has permanent water- and stain-resistant properties.
Nano Touch is a trademark for one of their nanotechnologies for treating a “core-wrap” type of fabrics. Core is usually synthetic fibers wrapped with natural fibers, such as cotton. The (nano)-treated core component of a core-wrap bicomponent fabric provides high strength, permanent anti-static behavior, and durability, while the traditionally-treated wrap component of the fabric provides desirable softness, comfort, and aesthetic characteristics.
Nano Care technology is offered to produce wrinkle-free/resistant and shrink-proof fabrics made of cellulosic fibers, such as cotton.
Nano Dry technology, provides hydrophilic finishing to synthetic fabrics. This nano-based finish allows the fabric to whisk away the contact body’s moisture/sweat, which quickly evaporates to provide comfort to the wearer.
Nano beads are used into the textile substrate for carrying bioactive or anti-biological agents, drugs, pharmaceuticals, sun blocks, and textile dyes, which subsequently can provide desired high performance attributes and functionalities to the treated fabrics.
Source:
Nanofinishing, Adv. Text. Tech., 11, 4 (2002).
Beringer, J., and Hofer, D., Melliand Int., 10, 295 (2004).
De Meyere, T., Meyvis, T., Laperre, J., Poorteman, M., and Libert, D., Unitex, 4, 4 2004).
De Meyere, T. , Meyvis, T., Laperre, J., Poorteman, M., and Libert, D., Tinctoria, 101, 39 (2004).
A.P.S. Sawhney: Modern Applications of Nanotechnology in Textiles, Textile Research Journal Vol 78 (8): 731–739
(PDF) Nanotechnology Applications in Textiles. available from: https://www.researchgate.net/publication/322466138_Nanotechnology_Applications_in_Textiles [accessed Jan 21 2022].
Functionalization of the textiles using nanotechnology:
Nanotechnology is present in textile functionalization and by applying some of specific nano-solutions can cover several different special treatments. The aim is using 2% emulsion of nano-solution containing SiO2 by spraying method to impart water and oil repellency on three types of textile materials:
The first material is a fabric of characteristics: main and weft threads P/PE 67/33%, linear density 15 tex.
The second material is knitted fabric: thread one 100% P, linear density 20 tex, thread two 100% PE, linear density 20 tex.
The third test material has a nonwoven PE/ PP 50/50% strengthened by needle punching, area mass 340 g/m2.
Samples are dried at temperature of 20oC, humidity 50%, duration of 24h.
Water and oil repellence were determined by applying a drop of liquids with different surface tension using: paraffin, sunflower oil, milk, coffee and machine oil, see figures below:
Fig. 2.5.5. Photos of drops on the fabric before (A) and after processing (B): 1 - paraffin, 2 - sunflower oil, 3 - fresh milk, 4 - coffee, 5 - machine oil.
The first part (A) of the figure 2.5.5. shows the drop spilling and absorbing into the textile material, while after treatment with unlimited nano-solution, the drop is shaped like a "pearl". This is due to the reduction of the surface tension of the textile material, which proves the effectiveness of the treatment.
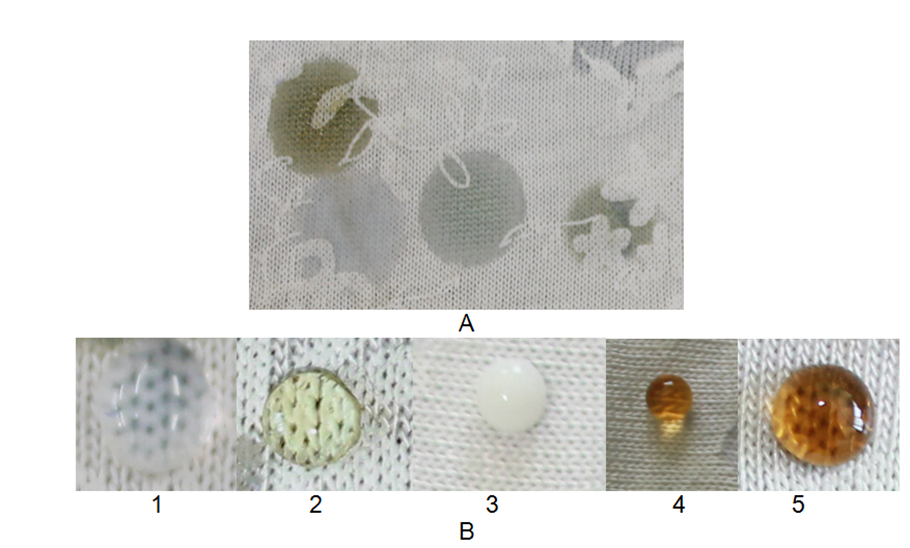
Fig. 2.5.6. Photos of drops on the knitted fabric before (A) and after processing (B): 1 - paraffin, 2 - sunflower oil, 3 - fresh milk, 4 - coffee, 5 - machine oil.
Despite
the larger pore diameter in the knitted fabric, the concentration used in
sample processing is sufficient to form a thin, protective layer on the fabric,
enveloping each fiber individually and thus protecting against the ingress of
water, coffee, milk, and grease. The reduction of the surface tension of the knitted fabric samples is also significant, given that this material is more porous than fabric.
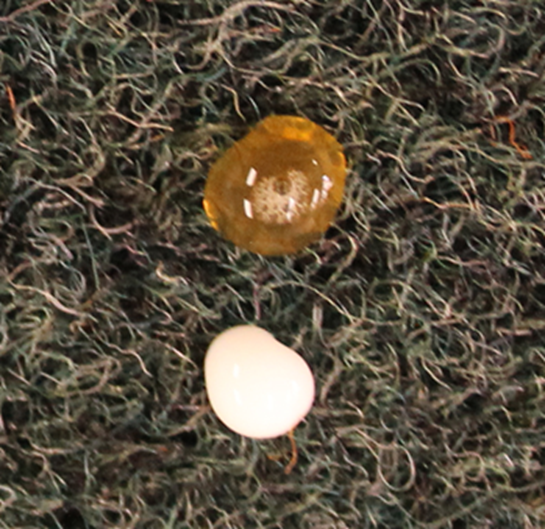
Fig. 2.5.7. Photos of drops on nonwovens after processing 1 - paraffin, 2 - sunflower oil, 3 - fresh milk, 4 - coffee, 5 - machine oil.
The third material, which has a fibrous structure, things are significantly different and the results after treatment of the material with nano-solution are presented in fig. 2.5.7.The nature of the structure does not allow the nano-solution to reach a large part of the fibers by the method of spraying and to form a sufficient protective layer. However, there is a retention of liquids from coffee and milk, which have a higher surface tension than oils. To achieve the full effect of application and film formation on most of the fibers, it is recommended to use another method of application - by full irrigation.
After determining the effectiveness of the applied nano-solution, the samples of materials 1 and 2 are washed at a constant temperature and variable time to determine the stability of the resulting film of nanoparticles on the fibers.
Fig. 2.5.8. Photographs of drops on fabric and knitted fabric after washing (at a temperature of 40 °C and a duration of 4 hours) samples, 1 - paraffin, 2 - sunflower oil, 3 - fresh milk, 4 - coffee, 5 - machine oil
According to research, washing process does not destroy the surface thin film as protective layer for oil and water repellency, consisted of nanoparticles inorganic 2% nano-solution of SiO2 and this treatment can be successfully used for clothing.
2.6. Spraying methods
Liquid Flame spray (LFS) is a flame pyrolysis technique that allows the simultaneous synthesis and deposition of noble metal and metal oxide nanoparticles in a continuous process. A precursor for the desired nanoparticles to be formed is injected into a high-temperature flame and the produced nanoparticles are deposited onto a substrate.
Fig. 2.6.2. Silver nanoparticles deposited onto the fabrics (Fabric I is a,b; Fabric II is c,d) before plasma coating (10X).
A plasma polymer coating was also deposited onto the nanoparticle coated fabrics for better adhesion of nanoparticles. HMDSO was selected for the plasma coatings due to its hydrophobicity, low toxicity and transparent optical properties with good chemical and electrical stability.The new ‘Touch’ test method that simulates the transfer of bacteria from one surface to another by touch was used for determining the antibacterial efficiency of the treated fabrics. The antibacterial results for both fabrics obtained from three repeated measurements are shown in figure below. Bacterial growth is evident in the reference samples that had no silver nanoparticles nor plasma coating. The growth of E. coli was inhibited in all the samples that had deposited silver nanoparticles. This was also the case even for samples with plasma coating on top of the nanoparticles. Since the antibacterial properties observed here are attributed to the release of silver, the plasma coating is either nonconformal, that is, it does not cover fully all the nanoparticles, or silver is released through the plasma coating or possible cracks in it. For gram-positive S. aureus, the coatings did not demonstrate antibacterial properties even for 20X coatings without any plasma coating on top.
K. J. Brobbey at al.: High-speed production of antibacterial fabrics using liquid flame spray, Textile Research Journal 2020, Vol. 90 (5–6) 503–511.
2.7. Layer by Layer deposition
Layer-by-Layer (LbL) is a thin film fabrication technique. The films are formed by depositing alternating layers of oppositely charged materials. The layers can be performed in different ways e.g. dip coating, spin-coating, spray-coating. Various materials can be deposited by LbL method including polyions, metals, ceramics, nanoparticles, and biological molecules.
The LbL assembling can be qualified as a good alternative approach to the well-known deposition methods, because it is versatile, inexpensive, and comfortable for use. The large advantage of LbL method is that is suitable for the formation of a uniform coating on curved surfaces. The whole process of multilayer structures buildup by LbL assembling, whose driving force, despite hydrogen bonding, covalent bonding, etc., is mainly electrostatic interaction between the oppositely charged species, usually consists of four steps (see Figure):

The applied positively charged polyelectrolytes are: polyallylamine hydrochloride (PAH), polyethyleneimine (PEI), polydiallyldimethylammonium chloride (PDDA),
The applied negatively charged polyelectrolytes are: polyvinyl sulfate (PVS), polyacrylic acid (PAA), or polystyrene sulfonate (PSS).
The LbL method is appropriate to obtaining organic/inorganic films with high accuracy by changing the number of multilayers, concentration and pH of the solution.
Today, the LbL self-assembling technique is an effective process to design drug delivery systems, capacitors, sensors, solar and fuel cells, quantum dots, catalysts with unique properties, using metal nanoparticles (Au, Ag, Pd, Pt), metal oxides incorporated into appropriate polymer. Such metal nanoparticles with attractive optical, electronic, and catalytic properties are used in a broad range of applications ranging from physics to medicine.
Source: Thin Film Processes - Artifacts on Surface Phenomena and Technological Facet, Chapter 8, InTech Open.
A) Application of LbL method for preparing silica shell
LbL method is used for preparing silica shell with silica nanoparticles coated alginate microparticles by adding binder (PDDA), see on the figure bellow - on scheme of LbL deposition.
Fig. 2.7.2. Schematic presentation of producing silica-coated alginate particles by layer by čayer metods
Mechanism: producing of silica-coated alginate particles with specific controllable shell structure for applications in drug and other chemicals delivery. The silica shell is made by electrostatic Layer by Layer assembly of silica nanoparticles on the surface of alginate microparticles which are negatively charged as well as silica nanoparticles. The positively charged polyelectrolyte Polydimethyldiallylamonium chloride (PDDA) is used as a “binder”.
Dip coating method was used with following steps:
- PDDA (positively charged)
- Washing
- Silica np (negatively charged)
- Washing
Steps from 1. to 4. are repeated untill the functional coating reachs the desired thickness.
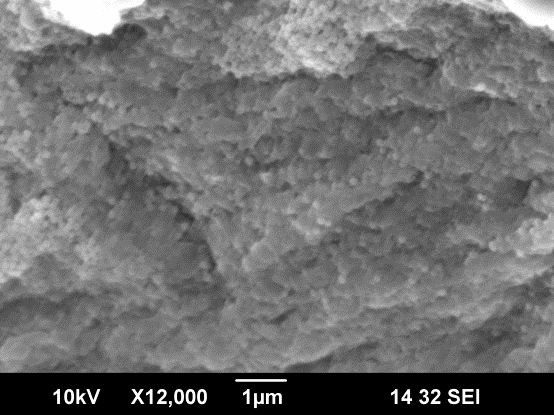
Fig. 2.7.3. SEM image of silica np deposited on alginate particle Fig. 2.7.4. Thickness of (PDDA/silica np) layers calculated from the QCM (by Quartz Crystal Microbalance)
Source: Layer-by-Layer method – Chobotix
Useful link:
B) Application of LbL method on textile substrate
Application of LbL method on textile materials in recent time considered as promising technique in achievement functional coatings on textile materials and attract great attention of different scientists.
Mechanism:
Research group consist of scientist from University of Science and Technology of China, are used the layer by layer (LbL) deposition of chitosan/melamine/urea (CS/ME/UREA) and phytic acid (PA) onto the acrylic acid (AA) grafted Polyamide 6.6 (PA 6.6) fabrics including a pad-dry-cure treatment with chitosan/graphene oxide (CS/GO) nanocomposites were considered to improve the hydrophilicity and durable flame retardancy, see schematic representation reaction below in the figure 2.7.5.:
Testing methods:
- Limiting oxygen index (LOI) value for flame retardancy,
- Melt dripping tendency,
- Peak Heat Release Rate (pHRR)
- Thermogravimetric analysis (TGA) test for thermal stability and char yield%,
- Hydrophilicity,
- Hybrid coatings stability after 10 home laundering cycles
Results:
- Hybrid coatings significantly improve the flame retardancy as the limiting oxygen index (LOI) value reached up to 25% from 18.5%,
- Completely stop the melt dripping where the fabric sample with two bilayers (2BLs) deposition and simultaneously treated with CS/GO nanocomposite (PA6.6-g-AA-2BL-CS/GO) achieved a V-1 rating.
- Two blayers (2BLs) deposited hybrid coating (i.e., PA6.6-g-AA-2BL-CS/GO) decreasing the Peak Heat Release Rate (pHRR) by 47.1%; a maximum reduction of pHRR by about 56% was achieved for five bilayers (5 BLs) deposition.
- Considerable improvement in thermal stability and char yield% were also realized in the thermogravimetric analysis (TGA) test. Furthermore, the as-prepared hybrid coatings imparted better hydrophilicity as a 2BLs deposition along with pad-dry-cure treatment by CS/GO could boost up the hydrophilicity of the treated fabrics further compared to the only 2BLs deposited fabric sample.
- Hybrid coatings could withstand against 10 home laundering cycles.
Source: M. Ziaur Rahman et al: Progress in Organic Coatings,144, Juy 2020, accessed at: https://doi.org/10.1016/j.porgcoat.2020.105640
Useful link: Cholesterol biosensors prepared by layer-by-layer technique, Biosensors & Bioelectronics 16 (2001) 849–8562.8. Biotechnological treatments
Biotechnological treatments
Disadvantages of enzymes: poor stability, poor compatibility with other chemical agents, longer processing time, relatively high cost.
Today, using of biomolecules is promising for treatment of synthetic fibers.
Group of researchers are used Polylysine (PLL ) biomolecule - as a surface coating agent for simultaneously imparting hydrophilic and antibacterial functions to PA fiber.
It well known that polyamide (PA) fiber possess lower hydrophilic properties and poor wearing comfort and without antibacterial function, but in the same time PA fiber is after polyester (PES) fiber, on the second place of applied fiber for production underwear, outerwear, sports/leisure wear and decorative fabrics.
Polylysine biomolecules are used to fabricate PA as material with the hydrophilic and antibacterial surface by a dip coating technique.
Chemical mechanism: The Schiff base reaction between the aldehyde groups of glutaraldehyde (used as crosslinker) and the amino groups of PLL and PA fiber was utilized to increase washing resistance.
Results: Final effects on the hydrophilicity of PA fabric were studied by the wetting time of water droplet, while the coating effect was further confirmed by water contact angle, moisture adsorption and capillary effect tests. The functional surface of the PLL coated fabric was proved by scanning electron microscope, X-ray photoelectron spectroscopy, and charge effect.
Conclusions: The PLL coated fabric exhibited excellent hydrophilic and antibacterial properties with good washing durability. This research suggests that PLL biomolecule can be used as a surface coating agent for imparting hydrophilic and antibacterial functions to PA fiber in the same time.
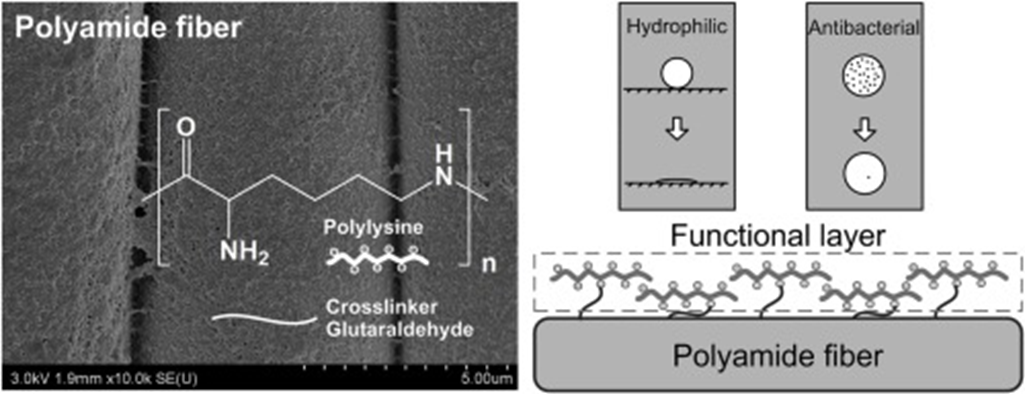
Source: W. Zhank et al.: Progres in Organic Coatings, 142, 2020, 105571, https://doi.org/10.1016/j.porgcoat.2020.105571
Surface of PLA sutures - high hydrophobicity - poor biocompatibility and cellular affinity.
Treatment: PLA sutures were etched by lipase firstly, and then grafted with chitosan - In order to increase the hydrophilicity (number of hydroxyl (-OH) bonds increase),
- the optimal conditions of treating PLA sutures by lipase were as follows: 45 Celzius degree reaction of temperature, 4.5 g/L concentration of lipase and 8 h reaction time.
- the optimal conditions of grafting chitosan onto PLA sutures were as follows: 4 h reaction time and 3 g/L concentration of chitosan. The chitosan grafted and loaded on the surface of PLA sutures, and in some areas of the sutures which led to a rough surface and large friction coefficient.
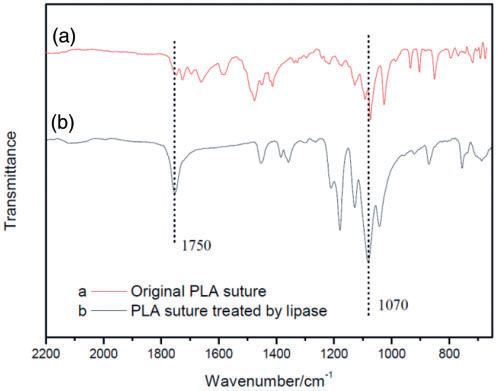
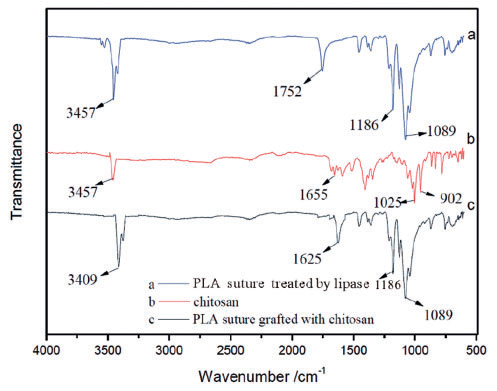
Fig. 2.8.2. FTIR: (a) original PLA suture; (b) PLA suture treated by lipase. Fig. 2.8.3. FTIR: (a) PLA treated by lipase; (b) chitosan, (c) PLA grafted with chitosan.
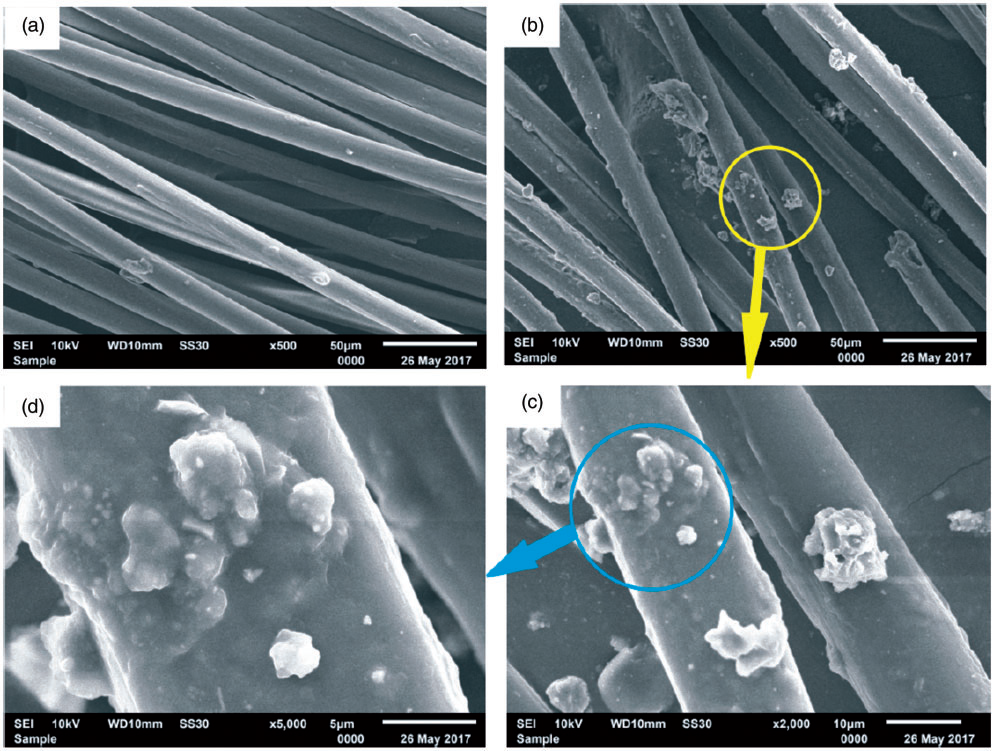
Fig. 2.8.4. SEM images of polylactic acid (PLA) sutures: (a) original PLA sutures; (b) PLA sutures grafted with chitosan (x500); (c) PLA sutures grafted with chitosan (x2000); (d) PLA sutures grafted with chitosan (x5000).
Source: Textile Research Journal 2019, Vol. 89(16) 3291–3302, sagepub.com/journals-permissions DOI: 10.1177/0040517518811936
Enzymatic Bleaching
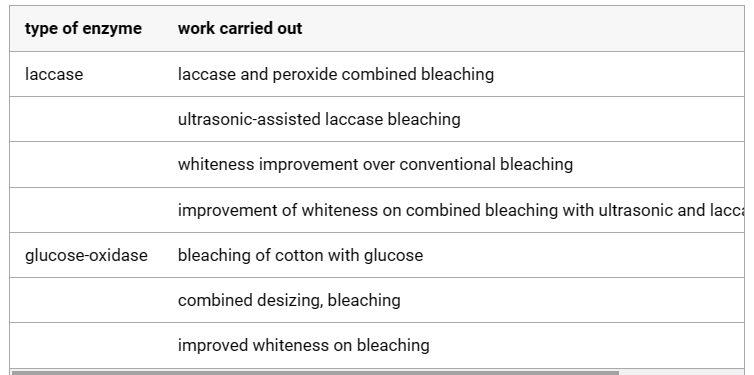
- Choudhury, A. K. R. Environmental Impacts of Denim Washing, Muthu, Subramanian Senthilkannan-Sustainability in Denim. In The Textile Institute Book Series; Woodhead Publishing, 2017; pp 49– 81. DOI: 10.1016/B978-0-08-102043-2.00003-4.
- Liu, X.; Kokare, C. Microbial Enzymes of Use in Industry. In Biotechnology of Microbial Enzymes; Brahmachari, G., Ed.; Academic Press, 2017; pp 267– 298. DOI: 10.1016/B978-0-12-803725-6.00011-X.
- Madhu, A.; Chakraborty, J. N. Developments in Application of Enzymes for Textile Processing. J. Clean Prod 2017, 145, 114– 133, DOI: 10.1016/j.jclepro.2017.01.013.
2.9. Mechanical treatments and auxetic materials
2.9.1. CalenderingTextile materials undergo mechanical processing by calendering under controlled conditions of heat and pressure, with the purpose of achieving different textures or effects in the fabric - the result: a more compact and flat fabric with a smoothing effect (smoothness).
Fig. 2.9.1. Calendering prpcess; schematic representation
Biopolishing
👉 1-s2.0-S0141391022000878-gr3_lrg.jpg (2917×3498) (els-cdn.com)
Source: A review on microplastic emission from textile materials and its reduction techniques - ScienceDirect
Read more in Critical Review on Sustainability in Denim: A Step toward Sustainable Production and Consumption of Denim | ACS Omega
2.9.2. Auxetic materials - helical auetic yarn (HAY)
Auxetic textiles have advanced rapidly in the past few decades due to their intuitive behavior of expanding laterally when subjected to a tensile stress. Performances of these materials such as a negative Poisson’s ratio always have increased shear stiffness, synclastic curvature (dome shaped), fracture toughness, and indentation resistance, especially for excellent energy absorption and damping properties what is suitable for their potential applications in the manufacture of advanced protective clothing (e.g. body armour, helmet, etc.), shape adaptive materials, and smart textiles.
Poisson’s ratio is a physical parameter, it is independent of the material scales, and auxetic behavior can be achieved from the molecular to macroscopic scale.
Preparation of auxetic fibers (yarn, fabric, composite) by creating auxetic geometries including helical, rope-like, honeycomb, and porous polymer-like structures or by combining with 3D printing, thermomechanical treatment, and chemical modification technologies are of great attention.
Construction steps of Auxetic materials
1. step:
HAY geometric structure is constructed by incorporating of two different components on a hollow-spindle covering system, as shown in Figure 1(a), and the geometric parameters of the HAY under different strain levels are defined in Figure 1(b) and (c). D and d defined the initial diameters of the core and wrap yarns.
Fig. 2.9.2. Preparation of auxetic fibers/yarns
2 step:
Fabrication of elastic woven fabrics based on HAYs
Weaving or knitting conventional yarns in an auxetic geometrical architecture and fabricating woven fabric through auxetic yarn directly are two main methods to create fabrics with auxetic behavior. Investigation of the auxetic behavior of fabrics, woven fabrics with different patterns is fabricated: plain weave and basket weave (2/2) were chosen to evaluate the effect of the structure on the auxetic properties of the fabric, a derivative weave with the warp and weft yarns arranged in a series of zigzag was designed also and showed at figures a, b, c) illustrated the 3D structure.
Figure 2.9.3. 3D structure design schematic: (a) plain weave; (b) basket weave; and (c) derivative weave.
3. step:
Measurement methods of properties of elastic woven fabrics could be realised using Tenstile test and Auxetic behavior test:
- Tensile test
The elastic woven fabrics were mechanically characterized for tension with reference to standard ASTM D3107-1975 and BS 4592-1992 on Tensile tester.
- Auxetic behavior test
To evaluate the NPR behavior of the as-fabricated fabric samples, firstly, a high-resolution camera (SONY A7R3) was placed on a tripod in front of the fabric tensile system. Five tests were carried out for each image in order to ensure higher accuracy of the NPR. The results were summarized and converted to NPR values based on equation (1). A square with a side length of 10mm was drawn in themiddle of each sample tomeasure the dimension change of the square, as shown in Figure (right)
Fig. 2.9.4. Schematic representation of auxetic material and testing of sample using tensile system
Source: Textile Research Journal 2020, Vol. 90(7–8) 809–823 DOI: 10.1177/0040517519881814
Auxetic materials can be used in composite materials to promote fiber reinforcement in textiles for crash helmets and sports clothing, as sponges, as ropes, in filtration and as shock absorbing materials.
They have a lot of
potential applications, from biomedical to automotive and
defense industries. Also, these materials could potentially
be used for completely new structures with special functions.
Generally, two approaches to producing auxetic textiles: the first one includes the use of auxetic fibers to produce an auxetic textile structure, whereas the other utilizes conventional fibers to produce an auxetic textile structure.
- Auxetic Polymers
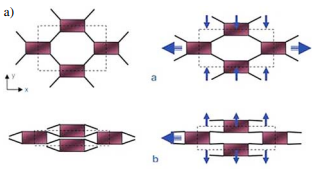
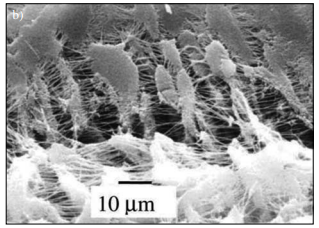
Fig. 2.9.5. left) Schematic representation of auxetic effect – fibrils act as hinges to cause the nodules to translate (a – conventional structure, b – auxetic structure) - left side, and Microstructure of expanded PTFE - right side (source: K. L. Alderson, Actual. Chim., 2012, 360, 73–77.).
Alderson and Evans presented a similar microstructure of a microporous form of ultra high molecular weight polyethylene (UHMWPE) produced by a novel thermoforming processing route. These polymers demonstrate Poisson’s ratios as low as –1.2, depending on the degree of anisotropy in the material.
A similar three-stage thermal processing route was used to engineer polypropylene and nylon also consisting of nodules interconnected by fibrils.
At the other hand, we have the polymers were produced with finely divided powder with a rough surface, by sintering and extruding the powder through a conical die. Powder morphology - particle shape, size, and surface roughness are critical variables for successful processing the auxetic behavior. The negative Poisson’s ratio values for such polypropylene polymers were up to –0.22 at 1.6% strain.
- Auxetic Fibers
Alderson et al. were the first to successfully produce auxetic fibers. They developed a kind of auxetic polypropylene (PP) fiber by employing a novel thermal processing technique, based on modified conventional melt spinning technique. This enabled a continuous fabrication process of auxetic polypropylene (PP) fibers. They used a laboratory scale melt extruder in place of a benchtop extruder and a flat profile of 159 °C across all zones of the extruder (source: K. L. Alderson, Actual. Chim., 2012, 360, 73–77).
Main approach: Production of auxetic fibers lies in maintaining the minimum draw ratio reported Ravirala (Phys. Stat. Sol. (b), 2005, 242, 653–664).
Partial melt extrusion technique could be used to produce auxetic fibers from polyester and nylon. Key processing parameter was extrusion temperature which played a critical role
in attaining the auxetic effect. Auxetic behavior of polyester fibers increased in the fibers processed at
a temperature of 225 °C, in comparison to fibers fabricated at 220 °C - the auxetic effect occurs over an extremely narrow temperature window. Such approch were applied to polypropylene and nylon fibers. This thermal processing technique result in lower modulus fibers which cannot be drawn to improve mechanical properties, but heat treatment improved the properties (strength) just enough to allow textile production, while limiting its overall effect. The reason for this kind of behaviour lies in the microstructure of the fibers.
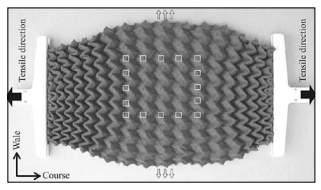
Fig. 2.9.6. Foldable weft knitted auxetic structure (source: Textile Res. J., 2010, 80, 856–863.)
Source: Auxetic Textiles, Acta Chim. Slov. 2013, 60, 715–723, Auxetictextiles-review_ACSI-4-2013.pdf
Examples of AUXETIC materials
👉 Useful link: Appl. Sci. 2018, 8(6), 941; https://doi.org/10.3390/app8060941
👉 Useful video:
👉 Useful video;
3. Functionalization of textiles using nanotechnology
In this chapter students/lerners will be introduce with functional properties of textiles based on novel technology and biomimetic approach from nature which will be by using appropriate techniqes transfered onto the textiles surface and structure. Learners will be informed how complex textile structure influenced on the treatment effectiveness and desired properties.The requirements for textile materials (and thus protective clothing and footwear) require continuous improvement of the production process of polymers, fibers, materials, clothing, footwear and equipment, which take on new properties and thus provide the necessary protective properties, such as:
- heat protection,
- flame protection,
- chemical protection,
- UV radiation,
- various radiation sources (ionized),
- reduction of tendency to static electricity (antistatic properties),
- anti-ballistic properties,
- mechanical hazards,
- resistance to microorganisms (bacteria, viruses),
- water repellent properties,
- waterproofing,
- and combinations of protective
properties.
It is well known that natural fibers like cotton which is a widely used fiber exhibits high absorbency, softness, and breathability, but relatively low strength, low durability, easy creasing and soiling, and flammability. Opposite of that, synthetic fibers can be antimicrobial and stain/crease-resistant but generally lack comfort as compared to cotton. The development of new fiber types that combine the advantages of both natural and synthetic fibers, as well as offering novel functions, has been desirable since the 1940s.
Customer demand for improved appearance color, shape, texture, aesthetic properties, and functionality has also increased. The applications of the functionalized textiles include medical monitoring of body function and metabolism, rehabilitation and electronic devices integrated into clothes. These technologies allow integrating sensors, flexible electronics and optical devices into textiles.
A new challenge in clothing technology is nanoengineered functional textiles.
The advantage of nanomaterials concerns creating function without altering of their comfort properties. Integrated materials and technologies offer a platform that responds to mechanical, chemical, electrical, thermal, optical, or magnetic stimuli. Wearable devices may include sensors, data transmission, and processing units. These engineered materials should seamlessly integrate into garments and be flexible and comfortable while having no allergic reaction to the body.
A significant challenge in the textile industry is that conventional approaches to functionalize fabrics do not lead to permanent effects. For example, laundering decreases imparted functional effects. Hence, nanotechnology can play a part in introducing new and permanent functions to fabrics.
It is very important to know that the textiles can be nanoengineered to posses specific functions including hydrophobicity, conductivity, antibacterial properties, antiwrinkle properties, antistatic, and light guidance and scattering (Figure 3.1.) by using nanotechnology, and how these properties can be achieved without affecting breathability or texture.
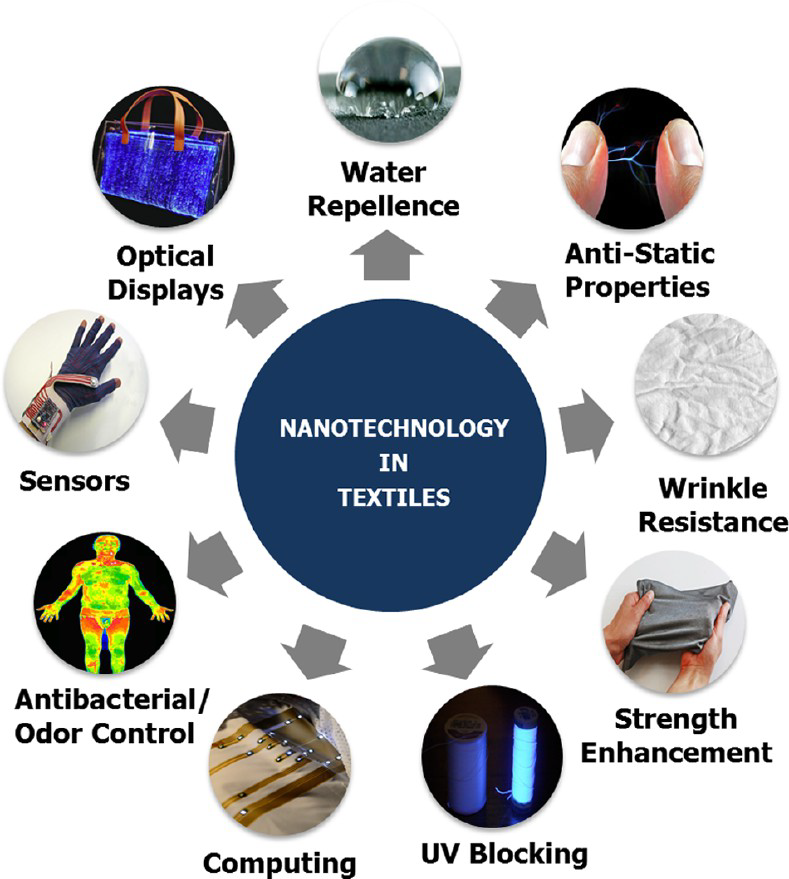
Fig. 3.1. Nanotechnology in textiles (reproduced from source: H. Saleem and S. J. Zaidi: Materials 2020, 13, 5134; doi:10.3390/ma13225134)
The manufacturing of functional
textiles can be classified into two groups:
- NANOENGINEERED TEXTILES
Water and Oil Repellence by forming Nano Whiskers - keep the fabric breathable. Nanowhiskers consisting of hydrocarbons that are 3 orders of magnitude smaller than a typical cotton fiber. Nanowhiskers are integrated within the fabric to create a peach fuzz effect. The spaces between individual whiskers are smaller than a drop of water but larger than water molecules, producing a high surface tension that allows the water to remain on the surface (like Lotus effect).
Examples of use of nano whiskers - keep fabric breathable
Fig. 3.2. Fabric with water and oil repellency, Superior durability, Fabric remains soft, natural wrinkle resistance.
Water repellence can also be induced through creation of 3D surface structures on the fabric by adding gel forming additives or coating the textile with nanoparticulate film.
In that case, the audio frequency (AC) plasma of fluorocarbon chemical was applied to deposit a nanoparticulate hydrophobic film onto a cotton fabric surface. The measurement of the contact angle showed that the superhydrophobicity of the cotton fabric was obtained with a treatment of only 30 s. Hydrophobic cotton fabric coated by a thin nanoparticulate plasma film and producing roughness on the surface of the fabric, superhydrophobicity can be created without affecting abrasion resistance and softness of the fabric.
Also, SiO2 nanoparticles (NPs) with water-repellent agents can ensure hydrophobicity to textiles. SiO2NPs (143−378 nm) were synthesized via a sol−gel process, and cotton fabrics after treatment with both of them have contact angles above 130°.
Hydrophobicity can be ensured with SiO2 which cotton surface make more roughness while the perfluorooctylated quaternary ammonium silane coupling agent (PQASCA) decrease surface energy, and resulted in water repellence with a water contact angle of 145°. Oil repellency of the fabric also improved, showing a 131° contact angle for a diiodomethane (CH2I2) droplet on the fabric surface.
Treatments organic–inorganic hybrid micro-nanoparticles
Silica dioxide nanoparticles (SiO2) were synthesized and functionalized with n-octadecyltriethoxysilane (OD) through a modified Stöber method for the preparation of organic–inorganic hybrid micro-nanoparticles - applied onto the polyester (PET) fabric via a conventional “dipping–drying” process for the fluoro-free water-repellent textile materials.
Mechanism:
Fig. 3.3. Mechanism of PET fabric for fluoro-free water-repellent textile materials by “dipping–drying” process
The coated PET fabric surface showed micro/nano-structures and exhibited hydrophobic behavior with water contact angle of 141°. PET hydrophobic fabrics exhibited excellent self-cleaning properties with dyes on the fabric surface (see figures below):
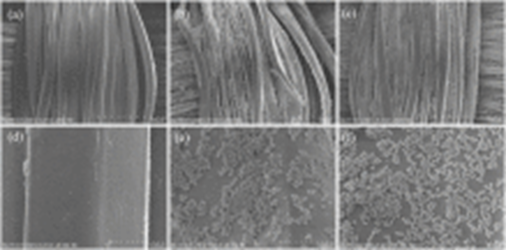
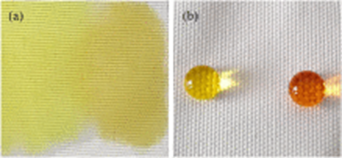
Fig. 3.4. SEM images of coated PET fabric surface showed micro/nano-structures Fig. 3.5. PET fabric before and after treatment
Source: https://doi.org/10.1016/j.jiec.2019.12.016
Antibacterial
textiles
- Ag, TiO2, and ZnO NPs are most common agents to impart antibacterial and fungicidal properties to textiles.
The antiseptic mechanism of Ag NPs is based on reacting with proteins in these organisms and adversely affecting their cellular function and inhibiting cell growth. They also reduce respiration, limiting the activity of the basal metabolism of the electron transfer system, and substrate transport into the cell membrane. When Ag NPs contact with moisture or bacteria, they adhere to the cell wall and membrane.
Fig. 3.6. Schematic representation of Ag+ ions action on bacteria destroying on textiles
The Ag+ ions are reactive (Ag NPs in their metallic state are inert, and they need to be ionized in the presence of moisture) and they diffuse through the cell wall and membrane into the cytoplasm. Ag+ ions bind to sulfur-containing proteins on the cell membrane to structurally change the cell wall. These structural changes result in the release of the cellular components to extracellular fluid due to the changes in the osmotic pressure. Additionally, the Ag+ ions bind to phosphate containing proteins to condense DNA, leading to a reaction with thiol group proteins to cause cell death. They also suppress the function of enzymes and inhibit the cell to produce ATP.
Fig 3.7. SEM images of Ag NPs on cotton fibers
Source: DOI: 10.1021/acsnano.5b08176
TiO2 NPs represent a usuful agent for textiles with antibacterial properties, of its photocatalytic activity. After illumination process with light with energy higher than its band gap (3.2 eV), TiO2 represent a photocatalyst after illumination process with light with energy higher than its band gap (3.2 eV), and has ability to have its electrons jump from the valence band to the conduction band. On the surface of the photocatalyst, where the electrons and oxygen form O2 and with water hydroxyl radicals. Unstable substances on the surface of the photocatalyst are oxidized into CO2 and water. Through this mechanism, the photocatalysts decompose organic matter including odor molecules, bacteria, and viruses.
ZnO NPs also represent agent with antibacterial properties. When ZnO NPs (about 25 nm) were coated onto textiles showed self-cleaning properties in the presence of bacterial species Gram-negative Escherichia coli and Gram positive Staphylococcus aureus.
Source: ACS Nano 2016, 10, 3042−3068 DOI: 10.1021/acsnano.5b08176 ACS Nano 2016, 10, 3042−3068
Textiles with Antistatic properties
The most common particles with antistatic properties for textile applications (especially for synthetic fibers) are TiO2, Ag NPs, ZnO whiskers and antimony (Sb)-doped tin oxide (SnO2) particles. Characteristics of such materials are electrically conductive and dissipate the static charge accumulated on the textile. It well known that synthetic materials like polyamide, polyester, and other synthetic polymers have high static charge because of their low hydrophilicity, while cellulose fibers have a high level of hydrophilicity and moisture content and have low level of static charge.
Except mentioned particles with antistatic properties, silane nanosol enhances antistatic properties by absorbing moisture in the air through hydroxyl groups.
ZnO NPs prepared by direct precipitation using zinc chloride (ZnCl2), were immobilized on polyester fabrics with antistatic finishing agent using a pad-dry-cure process. Results shows how the charge density of polyester fabrics was reduced from 58 to 0.95 (units in ×10−7 C m−2). With higher concentration of ZnO NPs in the finishing agent, the antistatic properties of the fabric decreased due to reduced dispersion of NPs.
Studies were shown how Ag NPs with fluorine water repellent finish can achieved antistatic charges with hydrophobicity on polyester fabrics.
Sb-NP-doped SnO2 particles were utilized to impart antistatic properties during preheating of bath which consist particles dispersed in water using polyethylenimine (PEIN), for spinning of polyacrylonitrile (PAN) fibers. The particles diffused into the fibers during spinning process created electrically conductive channels, which produced antistatic properties.
Wrinkle Resistance
Traditionally, fabrics are impregnated with resin to impart wrinkle resistance to textiles, but this decreases the tensile strength of the fiber, abrasion resistance, and dyeability while inducing hydrophobicity.
Today, carboxylic acids, such 1,2,3,4-butane tetracarboxylic acid (BTCA) and succinic acid (SA) as cross-linking agents were used to form cross-links between cellulose molecules and the acidic groups with TiO2 NPs. Carboxylic-acid treated fabrics with TiO2 NPs were softer compared to untreated fabric. TiO2 through its catalytic property can be used as a cocatalyst with sodium hypophosphite (NaPO2H2) to treat cotton with 1,2,3,4-BCTA, resulted in the wrinkle recovery of the cotton fabric. However, tear and tensile strength of the cotton fabric decreased due to the presence of TiO2 NPs.
Bombyx mori silk was also treated with TiO2 NPs in chitosan by cross-linking reactions of citric acid and maleic anhydride. Dry and wet delay-wrinkle recovery angles of the treated silk were 267 and 250° compared to untreated fabric of 235° and 178°. Additionally, SiO2 NPs and maleic anhydrate as a catalyst couled improve wrinkle resistance of silk.
Strength Enhancement
The most usufull way for producing fibers of improve strength is spinning technology. Through the melt-spinning technology, CNT-reinforced polymer composite fibers have been developed from polypropylene and carbon particles to improve strength, toughness and to decrease weight, but it is also possible during melt extrusion produce a wide range of nanoadditive yarns with improved mechanical properties and textures.
Wet-dry spinning or jet melt-spinning processes through spinnerets have been used to produce ordinary and fine denier textile fibers (1-100 μm in diameter). Nanoscale fibers require electrospinning, in which a solution is extruded through nanoscale spinnerets and the spun fibers are collected on a grounded plate. The fiber strength and conductivity can be increased by post-treatment approaches (e.g., heat).
Coagulation-based CNT electrospinning technology with controlling the fiber diameter and increasing twist, could be used for production of synthetic nanofibers. In this case we talk about composite fibers which are consist of 5-20 multiwalled CNTs. Such obtained highly twisted yarns posseses high strength, toughness, and energy damping capability for application in electronic textiles including actuators, electrostatic discharge protection, energy storage, heating, and radio and microwave absorption. The integration of CNTs into fibers certainly improve the strength and performance. For example, superaligned arrays of CNTs have a Young’s modulus in the TPa scale, tensile strength of 200 GPa, breaking strain of 20%, and elastic stain of 5%.
Beside the spinning process of forming fibers with improved strength properties, dipping and coating methods can be utilized to immobilize CNTs on cotton substrate. Prior to applying of treatments process, CNTs were modified with poly(butylacrylate) using surface grafting, and this composite was applied to cotton fabrics by dipping, drying, curing, and finishing treatments (see fig. 3.8. below).
Fig. 3.8. SEM images of CNT-coated on the cotton fibers
Source: DOI: 10.1021/acsnano.5b08176
The tensile strength of the CNT-coated cotton fabrics was improved along the weft and warp directions, showing enhancement in both loading capability and flexibility (displacement). For example, the tensile strength of the CNT-coated cotton was 0.5 kN at 13.5 cm displacement as compared to 0.25 kN for untreated fabrics.
UV Blocking
Most of textiles fibers both natural and synthetic are not resistant on Sunlight, esspecially on UV radiation. Because of that, additional finishing treatments, print and dyeing processes are important ans serve as protection of products during every day usage.
Inorganic UV blockers which aare nontoxic and chemically stable, operating at high temperatures. Nanoscale semiconductor oxides such as TiO2 and ZnO efficiently absorb and scatter UV radiation. At the nanoscale, scattering depends on the wavelength and the size of the NP, where the scattering is inversely proportional to the wavelength of the fourth power of the wavelength. For example, to scatter UV light (200−400 nm), the optimum particle size is 20−40 nm. Sol−gel method can be used to form a thin layer of TiO2 on the surface of the treated cotton. The UV protection effect may be maintained up to 50 launderings.56 Furthermore, ZnO nanorods (10−50 nm) have been incorporated in cotton to induce scattering at a high UV protective factor rating.
Fig. 3.9. SEM image of ZnO nanorods grown on cotton fibers (Reprinted from: Inorg. Chem. 2005, 44, 3926−3930)
3.1. Functional membranes of protective properties
Thermophysiological comfort while wearing such clothing is achieved by using a special membrane, eg Gore Tex®, Pro-line®, Sympatex® and others.
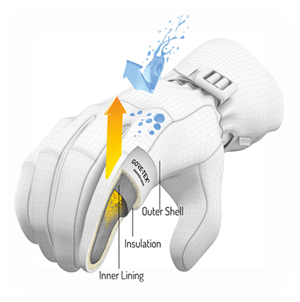
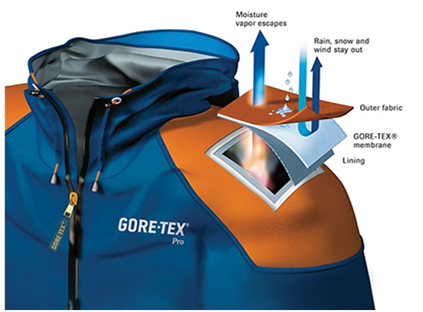
Characteristics of membrane:
- Micropore diameter - 0.2 μm (bacteria are about 4 times larger)
- They are resistant to chemicals and UV radiation, non-combustible, thermally stable between -250 ° C to + 280 ° C, biocompatible and degradable.
In commercial products, poly(tetrafluoroethylene) (PTFE) (W. L. Gore) developed an antistatic membrane that consisted of electrically conductive NPs anchored in the fibrils of the membrane. This membrane limited the formation of isolated chargeable areas and voltage peaks. This approach is advantageous over other antistatic agents since it does not wash off during laundry.
3.2. Biomimetics - applications in textile
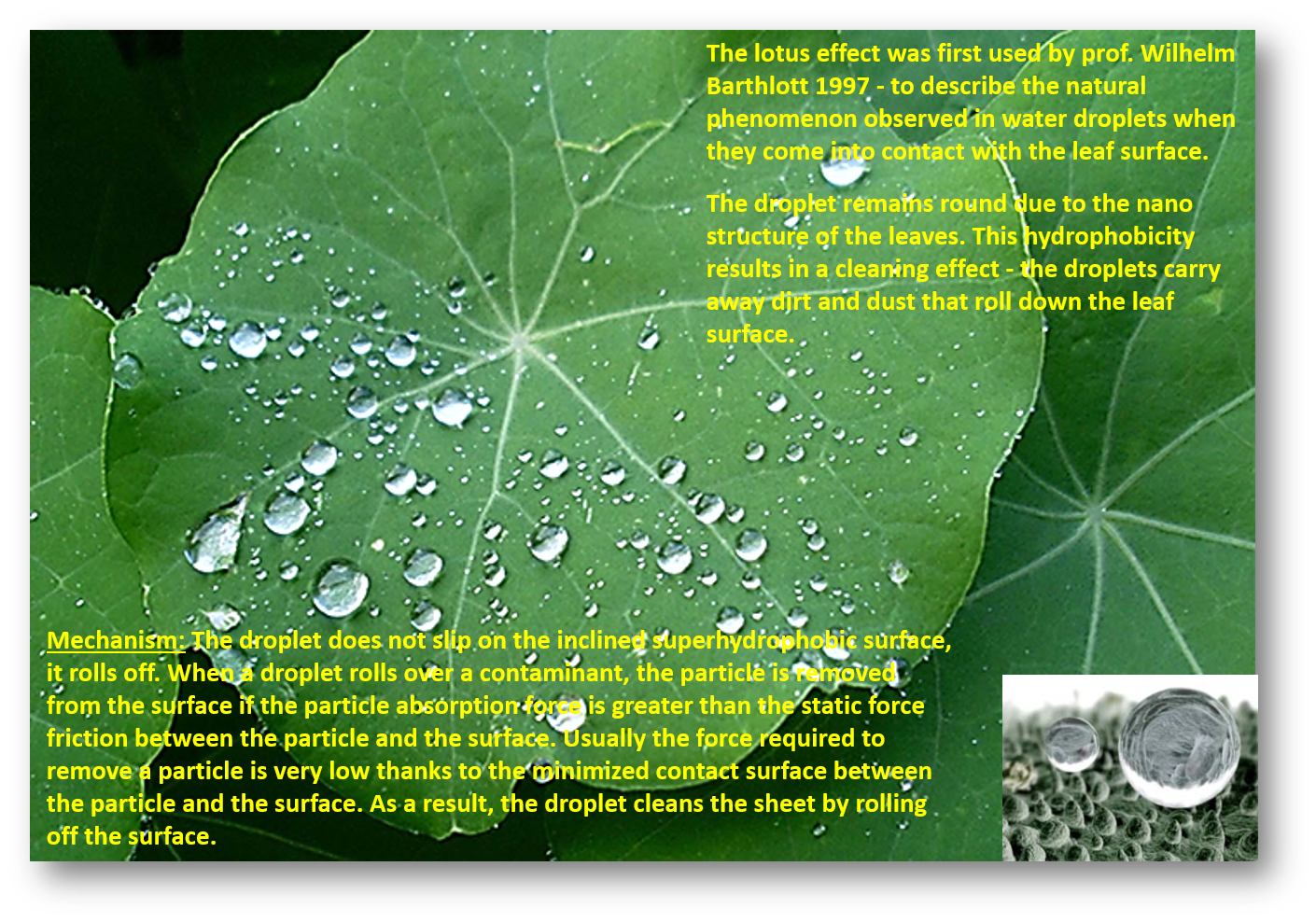
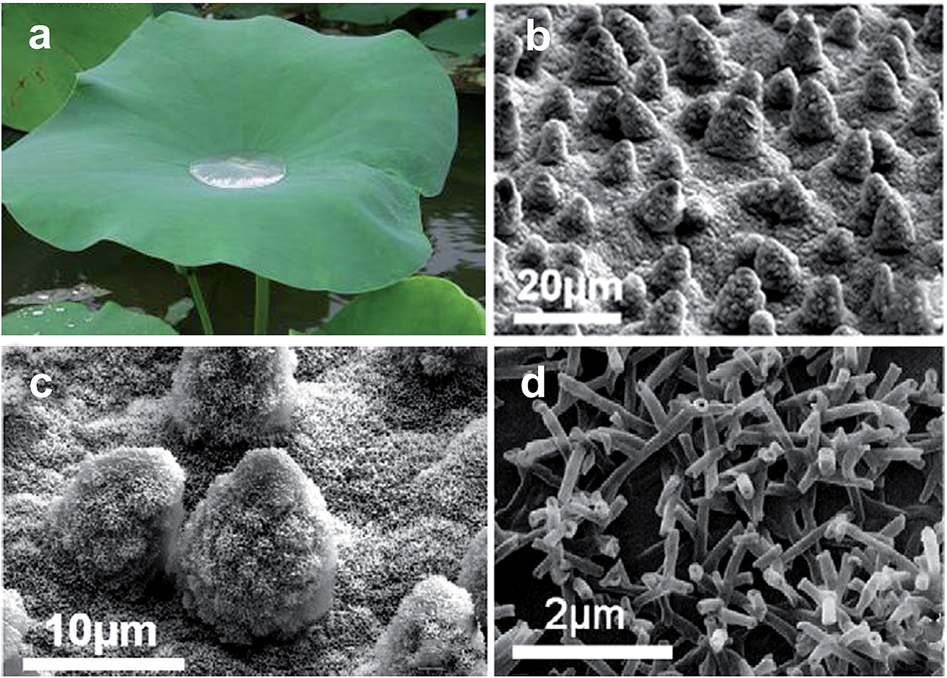
- for micro-scale fibre structure - coating of nanoscale particles onto the fibre surface to achieve the micro/nanoscale structure and post-fluorinate the hierarchical structure for the low energy;
- methods for preparing superhydrophobic textile surfaces include physical and chemical approaches, such as dip-coating, wet chemical deposition, electro-assisted chemical deposition, spraycoating, sol–gel, chemical etching, chemical vapour deposition, plasma processing, and polymer grafting.
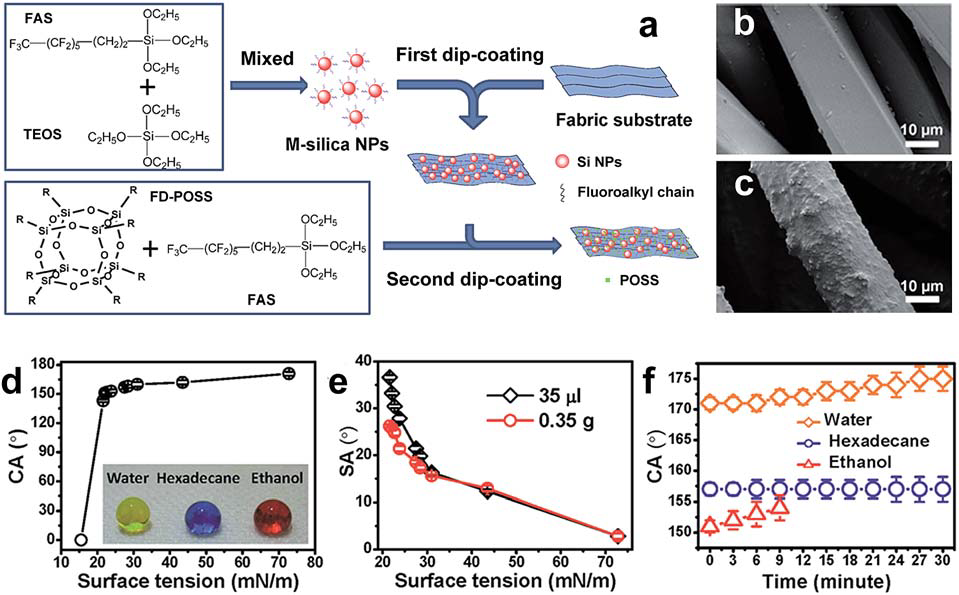
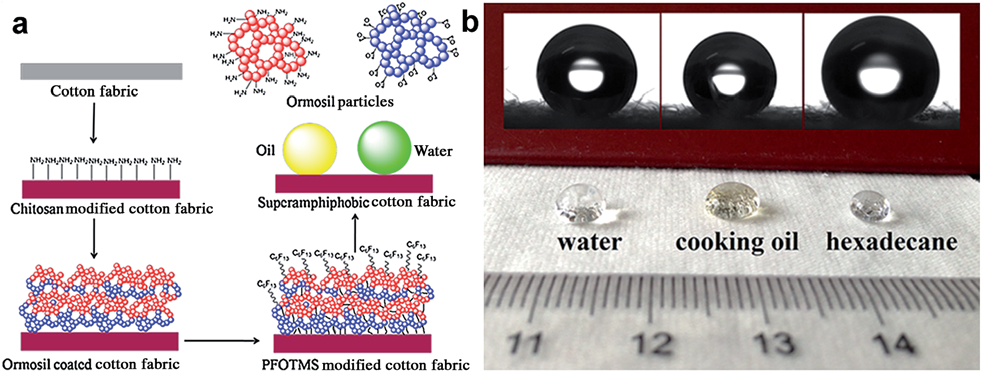
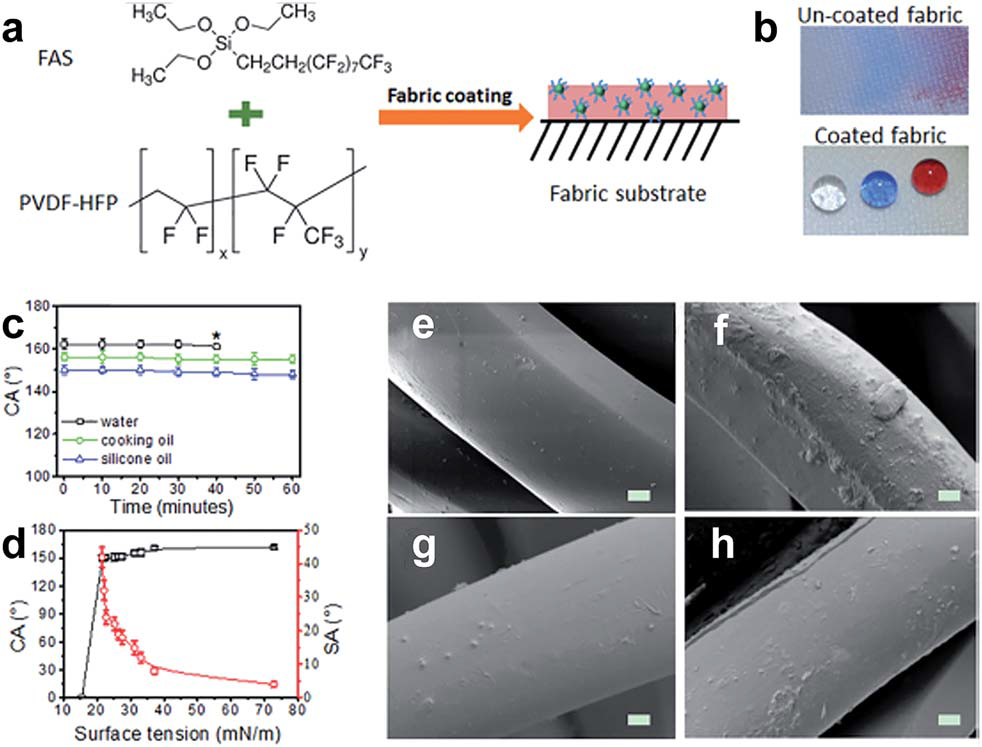
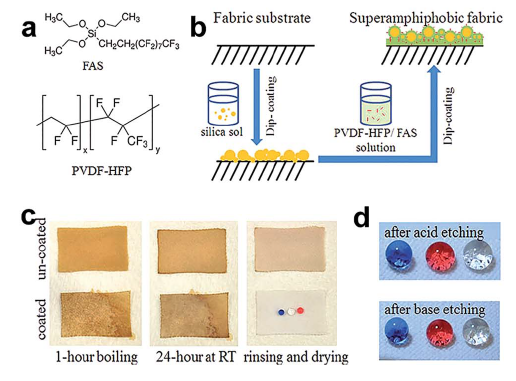
Photocatalytic self-cleaning fabrics
Photocatalytic process is the acceleration of photoreaction in the presence of catalyst. This process will decompose the dirt molecules by utilize the sunlight. The semiconductor photocatalytic process has shown a great potential as a low-cost, environmental friendly and sustainable treatment technology. Those semiconductor materials also have been used to functionalize onto the different textiles for self-cleaning properties. Another semiconductor material, which appears to be an alternative to TiO2 is zinc oxide (ZnO).
Fig. 3.2. . Photocatalytic self-cleaning fabrics mechanism
Photocatalytic
self-cleaning fabrics are able to clean themselves when exposed to light, but
they also possess antibacterial and UV blocking functions.
Source: doi:10.1088/1757-899X/133/1/012028
3.3. New technology in Textile industry environmentally friendly
TOXICITY OF NANOMATERIALS IN TEXTILES
Nowadays, the release of various nanoparticles to the environment is of more a concern. Huge problem are nanoparticles of Ag which are toxic to aquatic animals, including fish, crayfish, and plankton. Furthermore, the antibacterial properties of Ag NPs might disrupt the bacterial habitat in sewage treatment plants.
Nanowashing machines were shown to release Ag in effluent at a concentration of ∼11 μg L−1. Recent life cycle assessments involved comparing environmental benefits and negative effects of nano Ag T-shirts with conventional textiles treated with triclosan (a biocide), see below figure.
Fig. 3.3.1. Life cycle stages of nano Ag T-shirt with system boundaries
According to data, climate footprints of the manufacturing of nanoAg T-shirt were 2.70 kg of CO2-equiv for flame spray pyrolysis and 7.67−166 kg of CO2-equiv for plasma polymerization with Ag cosputtering. On the other side, conventional T-shirts produced by triclosan had emissions of 2.55 kg of CO2-equiv. Additionally, the toxic releases from washing and disposal stages had minor relevance.
Limitation of these studies was that variation in Ag release rates was not taken into consideration. Also, current life cycle impact assessment methods do not distinguish colloidally bound phases of metals. Until now, the life cycle assessments took into account only NP form. Considering other forms of nanomaterials, such as ionic forms, agglomerated forms, and oxidized forms, will provide improved of life cycle assessments. While these assessments provide an estimated effect of nanomaterials on the environment, public awareness holds importance in washing practices.
Efficient washing procedures using tumblers less and operating the washing machine at lower temperatures with appropriate detergents may reduce the environmental impact. The increase in the awareness for recycling rate of NP-embedded textiles may decrease the carbon footprint. The development of improved life cycle assessments will allow comparing nanoengineered textiles with conventional products in the market to prevent negative environmental consequences.
Source: Prospective Environmental Life Cycle Assessment of Nanosilver T-Shirts. Environ. Sci. Technol. 2011, 45, 4570−4578.
Fashionable functional products transcending the traditional functions of fabric are highly desirable. Growth in the fashion and entertainment industry is expected to contribute to overall market growth. Additionally, the demand from the sports and fitness sector has increased due to growing awareness about healthy lifestyles. End users participating in extreme sports, running, and skiing have also contributed to the demand for smart textiles. To increase the competitiveness with respect to Asia, the European Union has created initiatives for promoting incentives.
Today, global customers are willing to pay a premium price for functional garments. However, in another market segment, the target customer may demand affordable functional textiles. One possible reason for the interest in innovation in textiles is that porous materials, synthetic microfibers, and membranes used commercially over the past 30 years have been commodified. This may be attributed to the accessibility of blockbuster technologies due to patent expirations. The commodification subsequently reduced the profit margin and market share. As a result, companies in the textile industry need to offer competitive advantage through innovation by either enhancing performance or reducing the production cost.
Source: ACS Nano 2016, 10, 3042−3068, DOI 10.1021/acsnano.5b08176
Facts:
- In parallel to the development of nanotextiles, life cycle assessments and toxicity of released nanomaterials from textiles are being critically evaluated.
- Nanotechnology-based products will continue to emerge with new applications; manufacturers and regulatory agencies must ensure that these technologies will not have a negative effect on human health and the planet during their manufacture and life cycle.
- The textile industry is under scrutiny due its impact on climate change.
- Today, textiles and apparel account for ∼10% of the total carbon emissions. 17−20% of industrial water pollution originates from dyeing and finishing agents in the textile industry, negatively affecting people inhabiting regions around textile production plants, particularly in the developing world.
- Dyes and fixing agents (e.g., chromium) in textile manufacturers and tanneries are major pollutants, particularly in Southeast Asia.
- Hence, the effect of nanoproducts on the production dynamics and pollution remains questionable.
- Growing concerns among customers has begun forcing the manufacturers to reduce the environmental impact of their production methods, which will also involve the use of nanomaterials.
- Social awareness among customers has probed companies to invest in corporate social responsibility to offer environmentally sustainable products with reduced carbon footprints.
- These trends in customer behavior and climate change will include the use of nanotextiles, which need to be climate neutral and recyclable aimed at reducing greenhouse emissions.
- Nanotechnology will undoubtedly evolve textiles, transcending style changes to shape the next big concept: the connected couture.
Generally, environmental pollution in textile wet processes can be reduced by four main ways:
- process optimization (reducing in water, chemical energy consumption, and time loss),
- use of ecofriendly chemicals,
- reuse of water, and
- new technologies like ozone and plasma technologies, transfer printing, enzymatic processes etc.
Examples of Good practices:
- ECONYL® as material is made from rescued waste such as fishing nets and industrial plastic from oceans and landfills and converted into textile and carpet yarns for the fashion and interior industries
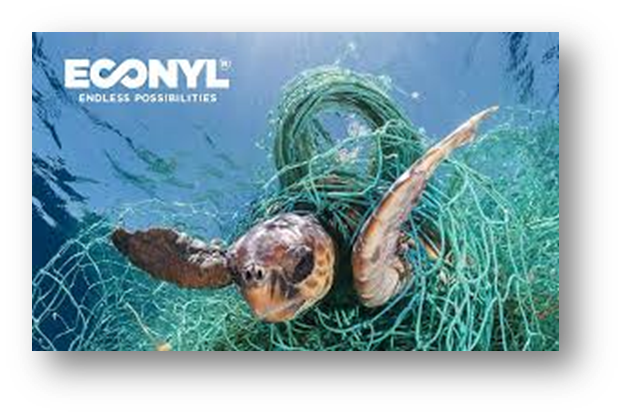
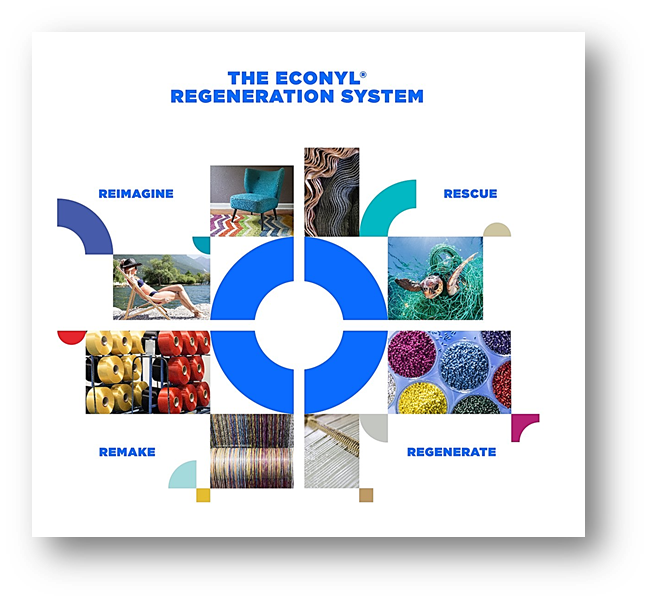
Source: https://arctic-flamingo.com/econyl-yoga-leggings/
ECONYL® 100% recycled PA, tt. Aquafil have potential in architecture, design, automotive industry and carpet industry.
- Lenzing™ Refibra™ fibre from cotton as waste raw materials

Source: https://www.sustainabletextiles.club/lenzing-refibra
Source: https://syvendeswimwear.com/pages/econyl👉 Critical Review on Sustainability in Denim: A Step toward Sustainable Production and Consumption of Denim

Here you can find new article as critical review on sustainability of denim:
The exponential development in knowledge on the health and environmental concerns linked to conventional denim processing is directly responsible for the continuous increase in demand for the exploitation of sustainable denim. Research is essential to explore alternative methods to reduce the environmental impact caused by these industries. This review examines the many sustainable ways to produce denim, keeping in mind the problems that the denim industry is now facing in finding alternatives to conventional manufacturing practices. The most current advancements in environmentally friendly dyeing techniques for denim have been extensively discussed. These processes include the production of indigo from bacteria as well as different dyeing processes, such as digital spray, microbially assisted dyeing, and foam dyeing denim with indigo. In addition, this review covers the many environmentally friendly finishing methods for denim garments, such as ozone fading, e-flow, enzyme-based bleaching, water, laser fading, and so on. Finally, it is described how the chemical and mechanical processes used to finish denim might affect the amount of microplastics and microfibers released from the denim garment during domestic washing. As a result, the content presented in this review aims to address the importance of sustainable denim processing, that is, something that can be rethought, reevaluated, renewed, and restructured within the scope of conventional denim processes, while taking eco-responsible solutions for increased environmental sustainability into account (Critical Review on Sustainability in Denim: A Step toward Sustainable Production and Consumption of Denim | ACS Omega).
Table: Various Sustainable Decoloration Methods for Denim Processing
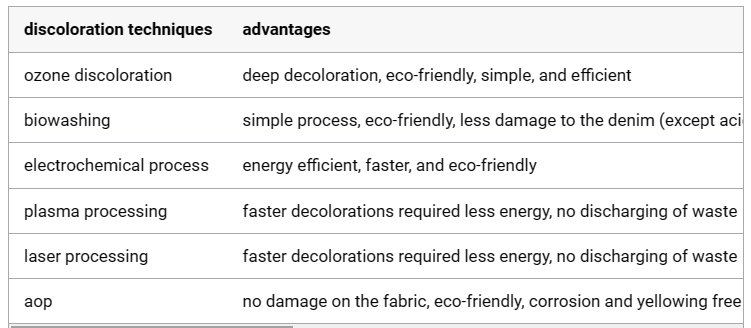
Source: https://pubs.acs.org/doi/10.1021/acsomega.2c06374
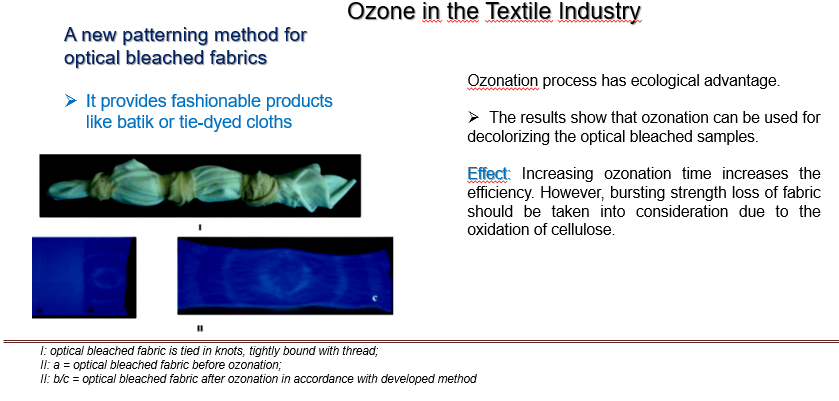
Source: Use of Ozone in the Textile Industry, DOI: http://dx.doi.org/10.5772/intechopen.81774
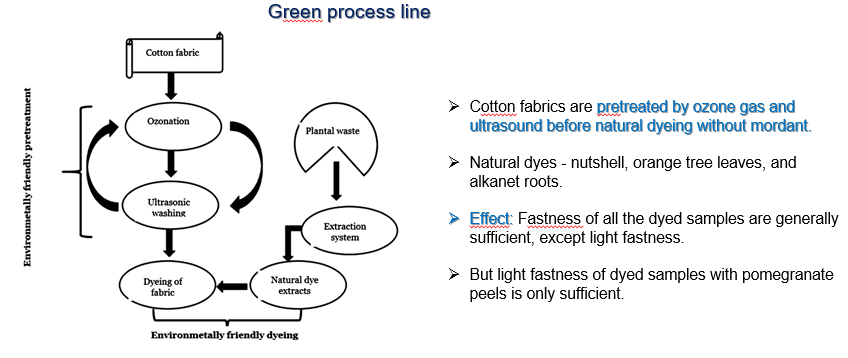
Source: Benli H, Bahtiyari Mİ. Combination of ozone and ultrasound in pretreatment of cotton fabrics prior to natural dyeing. Journal of Cleaner Production. 2015;89:116-124. DOI: 10.1016/j.jclepro.2014.11.007
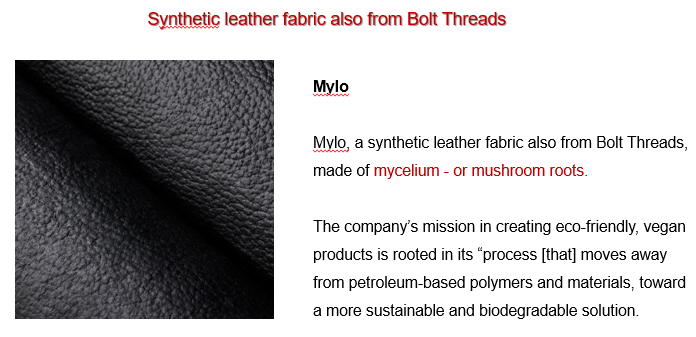