2. New technologies for textile functionalization
2.5. Nanotechnology in textile industry
Nanotechnology (NT) repersents a growing interdisciplinary technology often seen as a new industrial revolution.
NT deals with materials 1 to 100 nm in length. The fundamentals of nanotechnology lie in the fact that the properties of materials drastically change when their dimensions are reduced to nanometer scale.
Nowadays, the textile industry has discovered the possibilities of nanotechnology through understanding, manipulation, and control of matter at the above-stated length, such that the physical, chemical, and biological properties of the materials (individual atoms, molecules, and bulk matter) can be engineered, synthesized, and altered to develop the next generation of improved materials, devices, structures, and systems.
The main goal is - develop desired textile characteristics, such as high tensile strength, unique surface structure, soft hand, durability, water repellency, fire retardancy, antimicrobial properties, and the like.
Nanotechnology offering huge potential in a wide range of end uses and new properties of nano materials have attracted not only scientists and researchers but also businesses, due to their huge economical potential.
Nanotechnology also has real commercial potential for the textile industry;
- it can provide high durability for fabrics, because nano-particles have a large surface area-to-volume ratio and high surface energy, thus presenting better affinity for fabrics and leading to an increase in durability of the function.
- conventional methods used to impart different properties to fabrics often do not lead to permanent effects, and will lose their functions after laundering or wearing. In addition, a coating of nano-particles on fabrics will not affect their breath ability or hand feel.
Below, in the figures you can see the graphical representation of Nanotechnology application on textiles:
Fig. 2.5.1. Type of functional textiles based on nanotechnology (left)
Fig. 2.5.2. Textile application of nanotechnology (fight)
Application of nanotechnology:
- incorporation in fibres and yarns (fabrics),
- textile finishing by coating,
- e-textiles.
Nanoparticles can be introduced in the textile production process at two levels :
- during the melt extrusion of yarns nanoparticles based on clay, metal oxides or carbon nanotubes (CNTs) can be mixed in the polymer before the extrusion process, for obtaining:
- Antibacterial and Deodorant finishes
- Self cleaning clothes
- Water Repellent and Self Cleaning by Nano-Sphere
- during the coating - using padding process and after drying and curing the water compound evaporates; polymer was melted and spread over the surface resulting in uniform coating of fibre due to the nano size of the finishing agent.
A few representative applications of fabric finishing using NT are schematically displayed in figure 2.5.3.
Modification properties with nanoparticles as additive:
By combining the nano-particles of hydroxylapatite, TiO2, ZnO and Fe2O3 with other organic and inorganic substances, the surfaces of the textile fabrics can be appreciably modified to achieve considerably greater abrasion resistance, water repellency, ultraviolet (UV) resistance, and electromagnetic- and infrared-protection properties.
Titanium-dioxide nano-particles have been utilized for UV protection. Similarly, by using nanosized silicon dioxide as an additive in coating materials, significant improvements in the strength and flame-resistance of textile fabrics can be achieved.
Wrinkle resistance can be developed for cotton fabrics by using the nano-engineered cross-linking agents during the fabric finishing process, but also for eliminating toxic agents, while maintaining the desired comfort properties of cotton.
- e-textiles - smart/interactive textiles are materials and structures that sense and react to environmental conditions or stimuli, such as those from mechanical, thermal, chemical, electrical, magnetic or other sources.
Fig. 2.5.4. Warning Signaling - wearable txtiles
The sensors can monitor heart rate, respiration, and temperature. If vital signals were below critical values, a FLED would automatically display, for example, a flashing red light, and a wireless communication system could send a distress signal to a remote location.
Concepts of surface-engineered modifications through NT to develop certain high-performance fabrics, through trademarks:
- superior durability, softness, tear strength, abrasion resistance, and durable-press/ wrinkle-resistance
Nano-Pel technology for stain-resistance and oil-repellency treatments based on the concept of surface engineering and develops hydrophobic fabric surfaces that are capable of repelling liquids and resisting stains, while complementing the other desirable fabric attributes, such as breathability, softness, and comfort.
Nano-whiskers are nano-structures, provide roughness to the fabric surface so that fluid-surface interaction and consequently fluid penetration can be avoided - the treated fabric has permanent water- and stain-resistant properties.
Nano Touch is a trademark for one of their nanotechnologies for treating a “core-wrap” type of fabrics. Core is usually synthetic fibers wrapped with natural fibers, such as cotton. The (nano)-treated core component of a core-wrap bicomponent fabric provides high strength, permanent anti-static behavior, and durability, while the traditionally-treated wrap component of the fabric provides desirable softness, comfort, and aesthetic characteristics.
Nano Care technology is offered to produce wrinkle-free/resistant and shrink-proof fabrics made of cellulosic fibers, such as cotton.
Nano Dry technology, provides hydrophilic finishing to synthetic fabrics. This nano-based finish allows the fabric to whisk away the contact body’s moisture/sweat, which quickly evaporates to provide comfort to the wearer.
Nano beads are used into the textile substrate for carrying bioactive or anti-biological agents, drugs, pharmaceuticals, sun blocks, and textile dyes, which subsequently can provide desired high performance attributes and functionalities to the treated fabrics.
Source:
Nanofinishing, Adv. Text. Tech., 11, 4 (2002).
Beringer, J., and Hofer, D., Melliand Int., 10, 295 (2004).
De Meyere, T., Meyvis, T., Laperre, J., Poorteman, M., and Libert, D., Unitex, 4, 4 2004).
De Meyere, T. , Meyvis, T., Laperre, J., Poorteman, M., and Libert, D., Tinctoria, 101, 39 (2004).
A.P.S. Sawhney: Modern Applications of Nanotechnology in Textiles, Textile Research Journal Vol 78 (8): 731–739
(PDF) Nanotechnology Applications in Textiles. available from: https://www.researchgate.net/publication/322466138_Nanotechnology_Applications_in_Textiles [accessed Jan 21 2022].
Nanotechnology is present in textile functionalization and by applying some of specific nano-solutions can cover several different special treatments. The aim is using 2% emulsion of nano-solution containing SiO2 by spraying method to impart water and oil repellency on three types of textile materials:
The first material is a fabric of characteristics: main and weft threads P/PE 67/33%, linear density 15 tex.
The second material is knitted fabric: thread one 100% P, linear density 20 tex, thread two 100% PE, linear density 20 tex.
The third test material has a nonwoven PE/ PP 50/50% strengthened by needle punching, area mass 340 g/m2.
Samples are dried at temperature of 20 oC, humidity 50 %, duration of 24h.
Water and oil repellence were determined by applying a drop of liquids with different surface tension using: paraffin, sunflower oil, milk, coffee and machine oil, see figures below:
Fig. 2.5.5. Photos of drops on the fabric before (A) and after processing (B): 1 - paraffin, 2 - sunflower oil, 3 - fresh milk, 4 - coffee, 5 - machine oil.
The first part (A) of the figure 2.5.5. shows the drop spilling and absorbing into the textile material, while after treatment with unlimited nano-solution, the drop is shaped like a "pearl". This is due to the reduction of the surface tension of the textile material, which proves the effectiveness of the treatment.
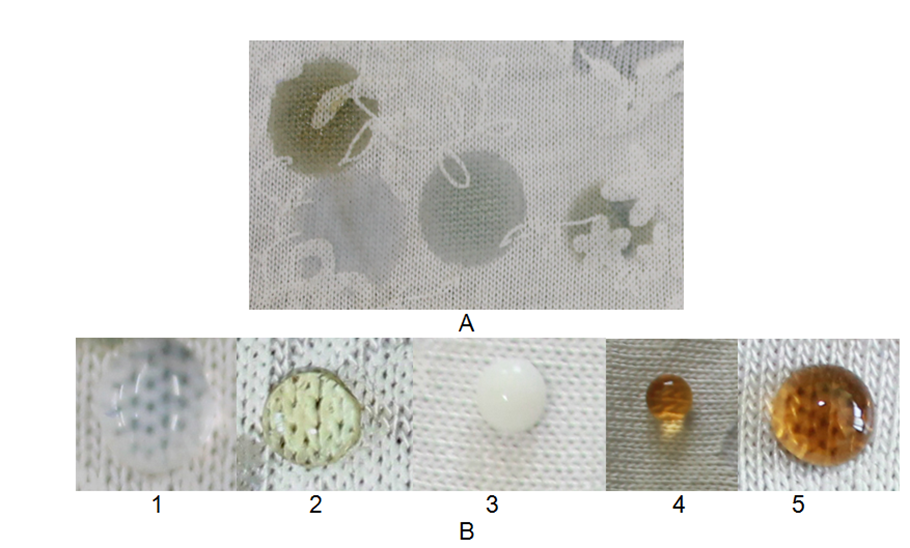
Fig. 2.5.6. Photos of drops on the knitted fabric before (A) and after processing (B): 1 - paraffin, 2 - sunflower oil, 3 - fresh milk, 4 - coffee, 5 - machine oil.
Despite the larger pore diameter in the knitted fabric, the concentration used in sample processing is sufficient to form a thin, protective layer on the fabric, enveloping each fiber individually and thus protecting against the ingress of water, coffee, milk, and grease. The reduction of the surface tension of the knitted fabric samples is also significant, given that this material is more porous than fabric.
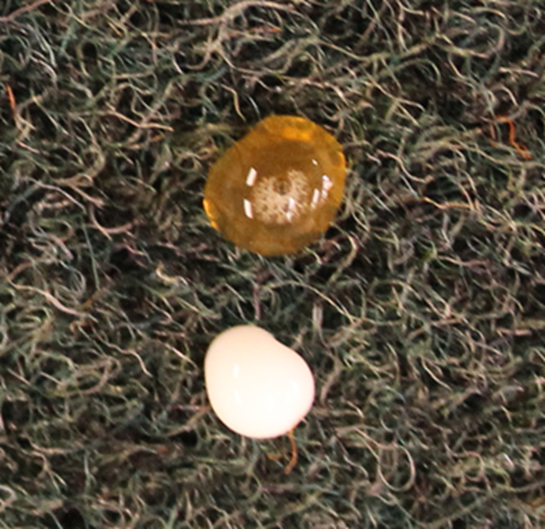
Fig. 2.5.7. Photos of drops on nonwovens after processing 1 - paraffin, 2 - sunflower oil, 3 - fresh milk, 4 - coffee, 5 - machine oil.
The third material, which has a fibrous structure, things are significantly different and the results after treatment of the material with nano-solution are presented in fig. 2.5.7.The nature of the structure does not allow the nano-solution to reach a large part of the fibers by the method of spraying and to form a sufficient protective layer. However, there is a retention of liquids from coffee and milk, which have a higher surface tension than oils. To achieve the full effect of application and film formation on most of the fibers, it is recommended to use another method of application - by full irrigation.
After determining the effectiveness of the applied nano-solution, the samples of materials 1 and 2 are washed at a constant temperature and variable time to determine the stability of the resulting film of nanoparticles on the fibers.
Fig. 2.5.8. Photographs of drops on fabric and knitted fabric after washing (at a temperature of 40 °C and a duration of 4 hours) samples, 1 - paraffin, 2 - sunflower oil, 3 - fresh milk, 4 - coffee, 5 - machine oil
According to research, washing process does not destroy the surface thin film as protective layer for oil and water repellency, consisted of nanoparticles inorganic 2% nano-solution of SiO2 and this treatment can be successfully used for clothing.