3. Functionalization of textiles using nanotechnology
The requirements for textile materials (and thus protective clothing and footwear) require continuous improvement of the production process of polymers, fibers, materials, clothing, footwear and equipment, which take on new properties and thus provide the necessary protective properties, such as:
- heat protection,
- flame protection,
- chemical protection,
- UV radiation,
- various radiation sources (ionized),
- reduction of tendency to static electricity (antistatic properties),
- anti-ballistic properties,
- mechanical hazards,
- resistance to microorganisms (bacteria, viruses),
- water repellent properties,
- waterproofing,
- and combinations of protective
properties.
It is well known that natural fibers like cotton which is a widely used fiber exhibits high absorbency, softness, and breathability, but relatively low strength, low durability, easy creasing and soiling, and flammability. Opposite of that, synthetic fibers can be antimicrobial and stain/crease-resistant but generally lack comfort as compared to cotton. The development of new fiber types that combine the advantages of both natural and synthetic fibers, as well as offering novel functions, has been desirable since the 1940s.
Customer demand for improved appearance color, shape, texture, aesthetic properties, and functionality has also increased. The applications of the functionalized textiles include medical monitoring of body function and metabolism, rehabilitation and electronic devices integrated into clothes. These technologies allow integrating sensors, flexible electronics and optical devices into textiles.
A new challenge in clothing technology is nanoengineered functional textiles.
The advantage of nanomaterials concerns creating function without altering of their comfort properties. Integrated materials and technologies offer a platform that responds to mechanical, chemical, electrical, thermal, optical, or magnetic stimuli. Wearable devices may include sensors, data transmission, and processing units. These engineered materials should seamlessly integrate into garments and be flexible and comfortable while having no allergic reaction to the body.
A significant challenge in the textile industry is that conventional approaches to functionalize fabrics do not lead to permanent effects. For example, laundering decreases imparted functional effects. Hence, nanotechnology can play a part in introducing new and permanent functions to fabrics.
It is very important to know that the textiles can be nanoengineered to posses specific functions including hydrophobicity, conductivity, antibacterial properties, antiwrinkle properties, antistatic, and light guidance and scattering (Figure 3.1.) by using nanotechnology, and how these properties can be achieved without affecting breathability or texture.
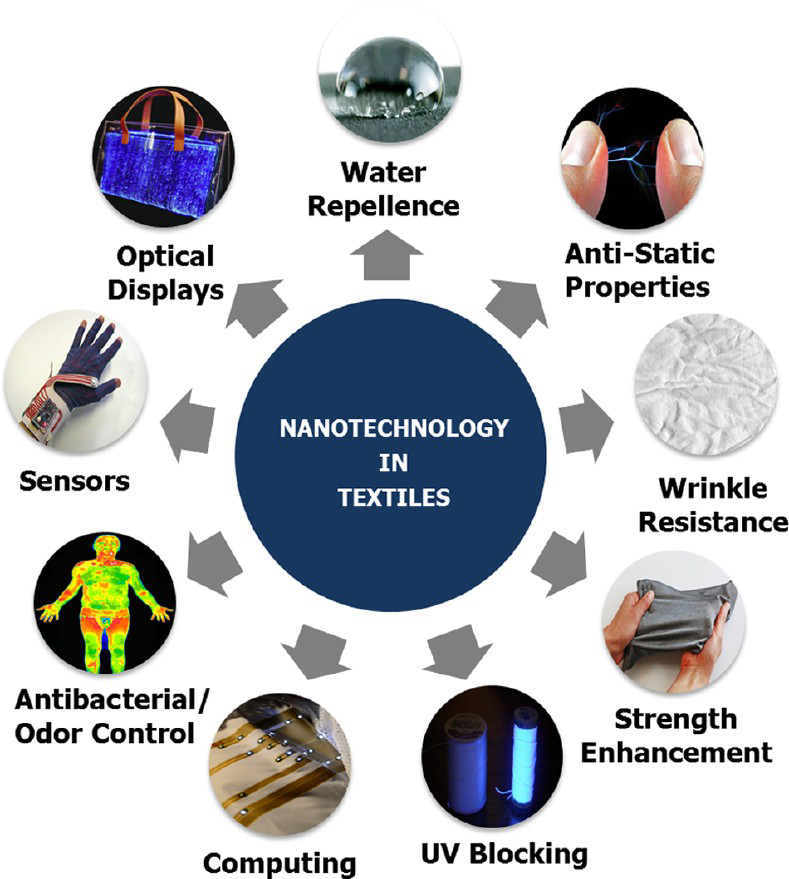
Fig. 3.1 Nanotechnology in textiles (reproduced from source: H. Saleem and S. J. Zaidi: Materials 2020, 13, 5134; doi:10.3390/ma13225134)
The manufacturing of functional
textiles can be classified into two groups:
2. The other is to modify the textile surfaces by functional biomaterials, resins, finishes.
- NANOENGINEERED TEXTILES
Water and Oil Repellence by forming Nano Whiskers - keep the fabric breathable. Nanowhiskers consisting of hydrocarbons that are 3 orders of magnitude smaller than a typical cotton fiber. Nanowhiskers are integrated within the fabric to create a peach fuzz effect. The spaces between individual whiskers are smaller than a drop of water but larger than water molecules, producing a high surface tension that allows the water to remain on the surface (like Lotus effect).
Examples of use of nano whiskers - keep fabric breathable
Fig. 3.2 Fabric with water and oil repellency, Superior durability, Fabric remains soft, natural wrinkle resistance.
Water repellence can also be induced through creation of 3D surface structures on the fabric by adding gel forming additives or coating the textile with nanoparticulate film.
In that case, the audio frequency (AC) plasma of fluorocarbon chemical was applied to deposit a nanoparticulate hydrophobic film onto a cotton fabric surface. The measurement of the contact angle showed that the superhydrophobicity of the cotton fabric was obtained with a treatment of only 30 s. Hydrophobic cotton fabric coated by a thin nanoparticulate plasma film and producing roughness on the surface of the fabric, superhydrophobicity can be created without affecting abrasion resistance and softness of the fabric.
Also, SiO2 nanoparticles (NPs) with water-repellent agents can ensure hydrophobicity to textiles. SiO2NPs (143−378 nm) were synthesized via a sol−gel process, and cotton fabrics after treatment with both of them have contact angles above 130°.
Hydrophobicity can be ensured with SiO2 which cotton surface make more roughness while the perfluorooctylated quaternary ammonium silane coupling agent (PQASCA) decrease surface energy, and resulted in water repellence with a water contact angle of 145°. Oil repellency of the fabric also improved, showing a 131° contact angle for a diiodomethane (CH2I2) droplet on the fabric surface.
Treatments organic–inorganic hybrid micro-nanoparticles
Silica dioxide nanoparticles (SiO2) were synthesized and functionalized with n-octadecyltriethoxysilane (OD) through a modified Stöber method for the preparation of organic–inorganic hybrid micro-nanoparticles - applied onto the polyester (PET) fabric via a conventional “dipping–drying” process for the fluoro-free water-repellent textile materials.
Mechanism:
Fig. 3.3 Mechanism of PET fabric for fluoro-free water-repellent textile materials by “dipping–drying” process
The coated PET fabric surface showed micro/nano-structures and exhibited hydrophobic behavior with water contact angle of 141°. PET hydrophobic fabrics exhibited excellent self-cleaning properties with dyes on the fabric surface (see figures below):
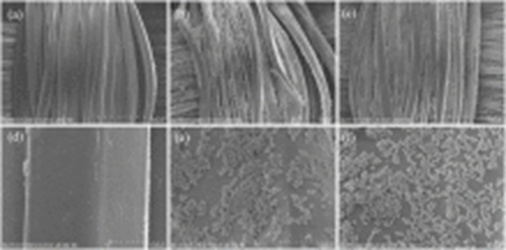
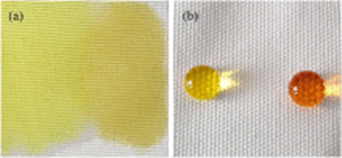
Fig. 3.4 SEM images of coated PET fabric surface showed micro/nano-structures Fig. 3.5 PET fabric before and after treatment
Source: https://doi.org/10.1016/j.jiec.2019.12.016
Antibacterial
textiles
- Ag, TiO2, and ZnO NPs are most common agents to impart antibacterial and fungicidal properties to textiles.
The antiseptic mechanism of Ag NPs is based on reacting with proteins in these organisms and adversely affecting their cellular function and inhibiting cell growth. They also reduce respiration, limiting the activity of the basal metabolism of the electron transfer system, and substrate transport into the cell membrane. When Ag NPs contact with moisture or bacteria, they adhere to the cell wall and membrane.
Fig. 3.6 Schematic representation of Ag+ ions action on bacteria destroying on textiles
The Ag+ ions are reactive (Ag NPs in their metallic state are inert, and they need to be ionized in the presence of moisture) and they diffuse through the cell wall and membrane into the cytoplasm. Ag+ ions bind to sulfur-containing proteins on the cell membrane to structurally change the cell wall. These structural changes result in the release of the cellular components to extracellular fluid due to the changes in the osmotic pressure. Additionally, the Ag+ ions bind to phosphate containing proteins to condense DNA, leading to a reaction with thiol group proteins to cause cell death. They also suppress the function of enzymes and inhibit the cell to produce ATP.
Fig 3.7 SEM images of Ag NPs on cotton fibers
Source: DOI: 10.1021/acsnano.5b08176
TiO2 NPs represent a usuful agent for textiles with antibacterial properties, of its photocatalytic activity. After illumination process with light with energy higher than its band gap (3.2 eV), TiO2 represent a photocatalyst after illumination process with light with energy higher than its band gap (3.2 eV), and has ability to have its electrons jump from the valence band to the conduction band. On the surface of the photocatalyst, where the electrons and oxygen form O2 and with water hydroxyl radicals. Unstable substances on the surface of the photocatalyst are oxidized into CO2 and water. Through this mechanism, the photocatalysts decompose organic matter including odor molecules, bacteria, and viruses.
ZnO NPs also represent agent with antibacterial properties. When ZnO NPs (about 25 nm) were coated onto textiles showed self-cleaning properties in the presence of bacterial species Gram-negative Escherichia coli and Gram positive Staphylococcus aureus.
Source: ACS Nano 2016, 10, 3042−3068 DOI: 10.1021/acsnano.5b08176 ACS Nano 2016, 10, 3042−3068
Textiles with Antistatic properties
The most common particles with antistatic properties for textile applications (especially for synthetic fibers) are TiO2, Ag NPs, ZnO whiskers and antimony (Sb)-doped tin oxide (SnO2) particles. Characteristics of such materials are electrically conductive and dissipate the static charge accumulated on the textile. It well known that synthetic materials like polyamide, polyester, and other synthetic polymers have high static charge because of their low hydrophilicity, while cellulose fibers have a high level of hydrophilicity and moisture content and have low level of static charge.
Except mentioned particles with antistatic properties, silane nanosol enhances antistatic properties by absorbing moisture in the air through hydroxyl groups.
ZnO NPs prepared by direct precipitation using zinc chloride (ZnCl2), were immobilized on polyester fabrics with antistatic finishing agent using a pad-dry-cure process. Results shows how the charge density of polyester fabrics was reduced from 58 to 0.95 (units in ×10−7 C m−2). With higher concentration of ZnO NPs in the finishing agent, the antistatic properties of the fabric decreased due to reduced dispersion of NPs.
Studies were shown how Ag NPs with fluorine water repellent finish can achieved antistatic charges with hydrophobicity on polyester fabrics.
Sb-NP-doped SnO2 particles were utilized to impart antistatic properties during preheating of bath which consist particles dispersed in water using polyethylenimine (PEIN), for spinning of polyacrylonitrile (PAN) fibers. The particles diffused into the fibers during spinning process created electrically conductive channels, which produced antistatic properties.
Wrinkle Resistance
Traditionally, fabrics are impregnated with resin to impart wrinkle resistance to textiles, but this decreases the tensile strength of the fiber, abrasion resistance, and dyeability while inducing hydrophobicity.
Today, carboxylic acids, such 1,2,3,4-butane tetracarboxylic acid (BTCA) and succinic acid (SA) as cross-linking agents were used to form cross-links between cellulose molecules and the acidic groups with TiO2 NPs. Carboxylic-acid treated fabrics with TiO2 NPs were softer compared to untreated fabric. TiO2 through its catalytic property can be used as a cocatalyst with sodium hypophosphite (NaPO2H2) to treat cotton with 1,2,3,4-BCTA, resulted in the wrinkle recovery of the cotton fabric. However, tear and tensile strength of the cotton fabric decreased due to the presence of TiO2 NPs.
Bombyx mori silk was also treated with TiO2 NPs in chitosan by cross-linking reactions of citric acid and maleic anhydride. Dry and wet delay-wrinkle recovery angles of the treated silk were 267 and 250° compared to untreated fabric of 235° and 178°. Additionally, SiO2 NPs and maleic anhydrate as a catalyst couled improve wrinkle resistance of silk.
Strength Enhancement
The most usufull way for producing fibers of improve strength is spinning technology. Through the melt-spinning technology, CNT-reinforced polymer composite fibers have been developed from polypropylene and carbon particles to improve strength, toughness and to decrease weight, but it is also possible during melt extrusion produce a wide range of nanoadditive yarns with improved mechanical properties and textures.
Wet-dry spinning or jet melt-spinning processes through spinnerets have been used to produce ordinary and fine denier textile fibers (1-100 μm in diameter). Nanoscale fibers require electrospinning, in which a solution is extruded through nanoscale spinnerets and the spun fibers are collected on a grounded plate. The fiber strength and conductivity can be increased by post-treatment approaches (e.g., heat).
Coagulation-based CNT electrospinning technology with controlling the fiber diameter and increasing twist, could be used for production of synthetic nanofibers. In this case we talk about composite fibers which are consist of 5-20 multiwalled CNTs. Such obtained highly twisted yarns posseses high strength, toughness, and energy damping capability for application in electronic textiles including actuators, electrostatic discharge protection, energy storage, heating, and radio and microwave absorption. The integration of CNTs into fibers certainly improve the strength and performance. For example, superaligned arrays of CNTs have a Young’s modulus in the TPa scale, tensile strength of 200 GPa, breaking strain of 20%, and elastic stain of 5%.
Beside the spinning process of forming fibers with improved strength properties, dipping and coating methods can be utilized to immobilize CNTs on cotton substrate. Prior to applying of treatments process, CNTs were modified with poly(butylacrylate) using surface grafting, and this composite was applied to cotton fabrics by dipping, drying, curing, and finishing treatments (see fig. 3.8. below).
Fig. 3.8 SEM images of CNT-coated on the cotton fibers
Source: DOI: 10.1021/acsnano.5b08176
The tensile strength of the CNT-coated cotton fabrics was improved along the weft and warp directions, showing enhancement in both loading capability and flexibility (displacement). For example, the tensile strength of the CNT-coated cotton was 0.5 kN at 13.5 cm displacement as compared to 0.25 kN for untreated fabrics.
UV Blocking
Most of textiles fibers both natural and synthetic are not resistant on Sunlight, esspecially on UV radiation. Because of that, additional finishing treatments, print and dyeing processes are important ans serve as protection of products during every day usage.
Inorganic UV blockers which aare nontoxic and chemically stable, operating at high temperatures. Nanoscale semiconductor oxides such as TiO2 and ZnO efficiently absorb and scatter UV radiation. At the nanoscale, scattering depends on the wavelength and the size of the NP, where the scattering is inversely proportional to the wavelength of the fourth power of the wavelength. For example, to scatter UV light (200−400 nm), the optimum particle size is 20−40 nm. Sol−gel method can be used to form a thin layer of TiO2 on the surface of the treated cotton. The UV protection effect may be maintained up to 50 launderings.56 Furthermore, ZnO nanorods (10−50 nm) have been incorporated in cotton to induce scattering at a high UV protective factor rating.
Fig. 3.9 SEM image of ZnO nanorods grown on cotton fibers (Reprinted from: Inorg. Chem. 2005, 44, 3926−3930)