3. Functionalization of textiles using nanotechnology
3.3. New technology in Textile industry environmentally friendly
TOXICITY OF NANOMATERIALS IN TEXTILES
Nowadays, the release of various nanoparticles to the environment is of more a concern. Huge problem are nanoparticles of Ag which are toxic to aquatic animals, including fish, crayfish, and plankton. Furthermore, the antibacterial properties of Ag NPs might disrupt the bacterial habitat in sewage treatment plants.
Nanowashing machines were shown to release Ag in effluent at a concentration of ∼11 μg L−1. Recent life cycle assessments involved comparing environmental benefits and negative effects of nano Ag T-shirts with conventional textiles treated with triclosan (a biocide), see below figure.
Fig. 3.3.1. Life cycle stages of nano Ag T-shirt with system boundaries
According to data, climate footprints of the manufacturing of nanoAg T-shirt were 2.70 kg of CO2-equiv for flame spray pyrolysis and 7.67−166 kg of CO2-equiv for plasma polymerization with Ag cosputtering. On the other side, conventional T-shirts produced by triclosan had emissions of 2.55 kg of CO2-equiv. Additionally, the toxic releases from washing and disposal stages had minor relevance.
Limitation of these studies was that variation in Ag release rates was not taken into consideration. Also, current life cycle impact assessment methods do not distinguish colloidally bound phases of metals. Until now, the life cycle assessments took into account only NP form. Considering other forms of nanomaterials, such as ionic forms, agglomerated forms, and oxidized forms, will provide improved of life cycle assessments. While these assessments provide an estimated effect of nanomaterials on the environment, public awareness holds importance in washing practices.
Efficient washing procedures using tumblers less and operating the washing machine at lower temperatures with appropriate detergents may reduce the environmental impact. The increase in the awareness for recycling rate of NP-embedded textiles may decrease the carbon footprint. The development of improved life cycle assessments will allow comparing nanoengineered textiles with conventional products in the market to prevent negative environmental consequences.
Source: Prospective Environmental Life Cycle Assessment of Nanosilver T-Shirts. Environ. Sci. Technol. 2011, 45, 4570−4578.
Fashionable functional products transcending the traditional functions of fabric are highly desirable. Growth in the fashion and entertainment industry is expected to contribute to overall market growth. Additionally, the demand from the sports and fitness sector has increased due to growing awareness about healthy lifestyles. End users participating in extreme sports, running, and skiing have also contributed to the demand for smart textiles. To increase the competitiveness with respect to Asia, the European Union has created initiatives for promoting incentives.
Today, global customers are willing to pay a premium price for functional garments. However, in another market segment, the target customer may demand affordable functional textiles. One possible reason for the interest in innovation in textiles is that porous materials, synthetic microfibers, and membranes used commercially over the past 30 years have been commodified. This may be attributed to the accessibility of blockbuster technologies due to patent expirations. The commodification subsequently reduced the profit margin and market share. As a result, companies in the textile industry need to offer competitive advantage through innovation by either enhancing performance or reducing the production cost.
Source: ACS Nano 2016, 10, 3042−3068, DOI 10.1021/acsnano.5b08176
Facts:
- In parallel to the development of nanotextiles, life cycle assessments and toxicity of released nanomaterials from textiles are being critically evaluated.
- Nanotechnology-based products will continue to emerge with new applications; manufacturers and regulatory agencies must ensure that these technologies will not have a negative effect on human health and the planet during their manufacture and life cycle.
- The textile industry is under scrutiny due its impact on climate change.
- Today, textiles and apparel account for ∼10% of the total carbon emissions. 17−20% of industrial water pollution originates from dyeing and finishing agents in the textile industry, negatively affecting people inhabiting regions around textile production plants, particularly in the developing world.
- Dyes and fixing agents (e.g., chromium) in textile manufacturers and tanneries are major pollutants, particularly in Southeast Asia.
- Hence, the effect of nanoproducts on the production dynamics and pollution remains questionable.
- Growing concerns among customers has begun forcing the manufacturers to reduce the environmental impact of their production methods, which will also involve the use of nanomaterials.
- Social awareness among customers has probed companies to invest in corporate social responsibility to offer environmentally sustainable products with reduced carbon footprints.
- These trends in customer behavior and climate change will include the use of nanotextiles, which need to be climate neutral and recyclable aimed at reducing greenhouse emissions.
- Nanotechnology will undoubtedly evolve textiles, transcending style changes to shape the next big concept: the connected couture.
Generally, environmental pollution in textile wet processes can be reduced by four main ways:
- process optimization (reducing in water, chemical energy consumption, and time loss),
- use of ecofriendly chemicals,
- reuse of water, and
- new technologies like ozone and plasma technologies, transfer printing, enzymatic processes etc.
Examples of Good practices:
- ECONYL® as material is made from rescued waste such as fishing nets and industrial plastic from oceans and landfills and converted into textile and carpet yarns for the fashion and interior industries
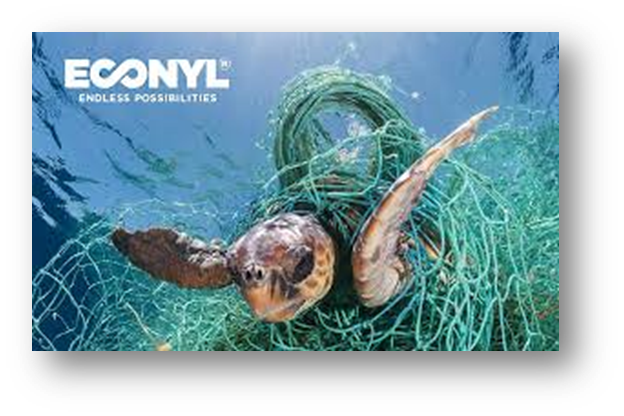
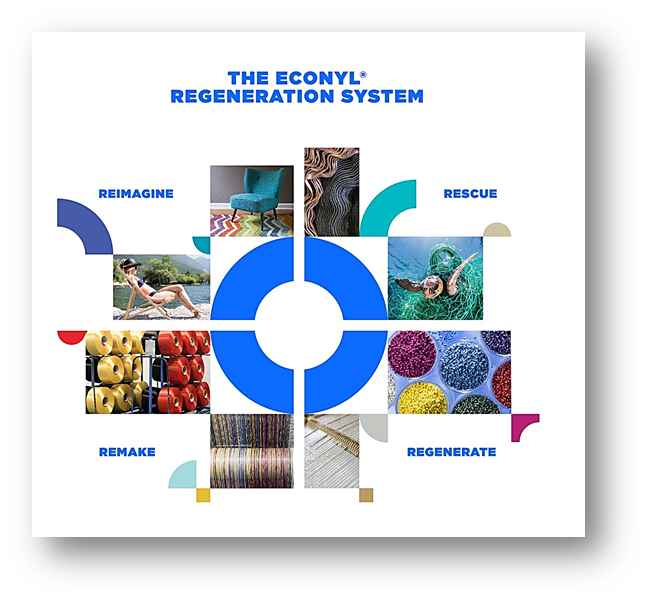
Source: https://arctic-flamingo.com/econyl-yoga-leggings/
ECONYL® 100% recycled PA, tt. Aquafil have potential in architecture, design, automotive industry and carpet industry.
- Lenzing™ Refibra™ fibre from cotton as waste raw materials

Source: https://www.sustainabletextiles.club/lenzing-refibra
Source: https://syvendeswimwear.com/pages/econyl
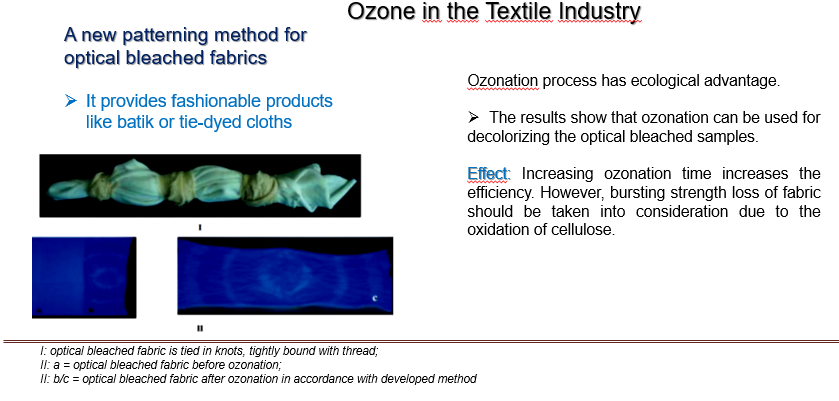
Source: Use of Ozone in the Textile Industry, DOI: http://dx.doi.org/10.5772/intechopen.81774
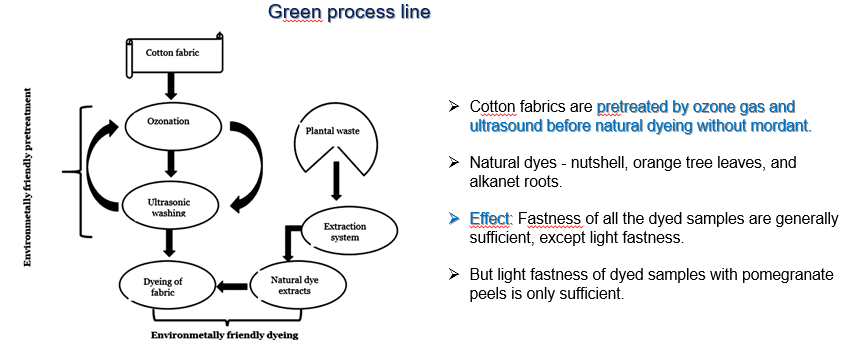
Source: Benli H, Bahtiyari Mİ. Combination of ozone and ultrasound in pretreatment of cotton fabrics prior to natural dyeing. Journal of Cleaner Production. 2015;89:116-124. DOI: 10.1016/j.jclepro.2014.11.007
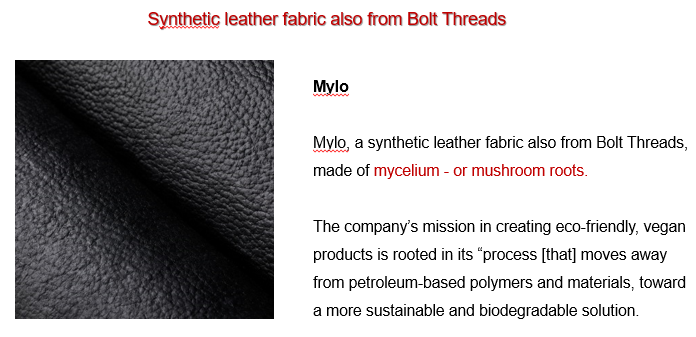