2. New technologies for textile functionalization
2.1. Plasma technology
Due to the increasingly stringent environmental requirements set in modern textile technology processes, increasing importance is attached to treatment by agents that are acceptable from an environmental point of view. In this sense, there has been more research related to the use of plasma as an environmentally friendly physical agent. Although known from before, a special interest in the application of plasma technology in the field of textiles has been recorded in the last ten years, especially in the processes of pre-treatment and finishing of textile materials for the purpose of obtaining multifunctional textile products. In this sense, the emphasis of modern treatment is focused on obtaining favorable effects by modifications of the fiber surface (textiles), which ultimately contribute to the overall quality of the textile material. Surface treatments with plasma, ozone, biopolymers, etc. which are being researched and implemented nowadays for the purpose of modifying the properties of textile materials, are, in addition to being environmentally friendly, also more energy efficient compared to conventional finishing methods. The development and commercialization of plasma technology in the design and production of modern textile materials contributes to reducing the use of chemical agents, which is gaining increasing importance - both from an environmental and economic point of view.
Plasma shapes and types are numerous and plasmas can be classified according to several criteria. Plasmas occurring in nature differ primarily in density (an order of magnitude of more than 10 exponents), and accordingly the differences in physical properties are extreme as well. A key parameter for distinguishing technical plasmas is the pressure of the neutral gas in which the ionized particles move relative to atmospheric pressure. According to this criterion, plasmas are classified into low-pressure, high-pressure and atmospheric pressure plasmas (atmospheric plasmas).
According to the temperature at which they are applied, plasmas are divided into cold and hot plasmas. Low-pressure plasma is an example of cold or low-temperature plasma, which is also an example of non-equilibrium plasma, which means that electrons in plasma have a much higher temperature than the temperature of heavier ion particles in plasma. With appropriate external gas excitation in such a plasma, it is possible to achieve conditions in which the gas temperature is close to room temperature, while the effective temperature and kinetic energy of the electron are much higher and large enough to maintain plasma and initiate plasma-chemical reactions. The temperature of the electrons Te is of the order of magnitude 104 to 105K, while the temperature of heavy particles of ions and other particles of molecules, atoms and free radicals is close to room temperature, so that the gas hardly heats up and maintains room temperature. Therefore, such plasma is particularly suitable for the treatment of thermally sensitive materials such as most textile materials.
In equilibrium plasmas there is a thermal equilibrium, i.e. the temperature of electrons and heavier ion particles is equal and usually high, and the kinetic energy of all particles is high. In a surface treatment application, such plasmas would be significantly more efficient in the production of radicals and the flow of ions coming to the surface of the material. However, since they develop a high temperature due to the high degree of ionization, it is very difficult to control the energy of particles and thus optimize the production conditions of specific radicals, and it is impossible to process thermally unstable materials. Such hot plasma is not suitable for textile applications, but is used in welding, thermal spraying, metal cutting and as a method for determining metals in water analysis.Cold plasma, both low-pressure plasma and atmospheric plasma, are suitable for textile applications. Low-pressure plasmas are obtained in a diluted gas whose pressure is significantly lower than atmospheric pressure, while atmospheric plasma is produced at normal atmospheric pressure. Therefore, a vacuum chamber or a vacuum pump is not required to obtain atmospheric plasma, while such equipment is necessary in the production of low-pressure plasma.
Plasma action mechanism
Plasma affects the surface of the substrate chemically and physically, with the reactions between the plasma and the surface depending on the type of gas used and its chemical properties. Textile materials subjected to such treatments undergo chemical and physical transformations related to chemical changes in the surface layer, changes in the structure of the surface layer and changes in the physical properties of the surface layer. Plasma creates a high density of free radicals during the dissociation of molecules during electron collisions and photochemical processes. This causes the destruction of chemical bonds in the polymer surface of the fiber resulting in the formation of new chemical entities. The action of plasma on the surface of fibers and polymers results in the creation of new functional groups such as –OH, –C=O, –COOH, which affect the improvement of the wettability of fabrics (hydrophilic effect), and can be active centers for graft polymerization of different molecules.
Therefore, plasma is primarily used for surface treatment of materials, because its action modifies only the surface properties to a layer thickness of only a few tens of nanometers, leaving the basic properties of the material almost unchanged. In this way, selective modification of fiber properties is achieved, e.g. it can affect the ability to wet and dye, adhesion characteristics, etc., which can hardly be achieved by classical chemical processes without affecting the basic properties of such processed fibers. In general, the action of plasma on the surface of a textile material can be roughly described through four groups of processes, Figure 1:
- Plasma cleaning of the surface,
- Plasma ablation or etching of the surface,
- Surface activation, plasma modification,
- Deposition, plasma polymerization.
Figure 1. Schematically shows these four types of actions and their effects in comparison with the untreated surface of the material.
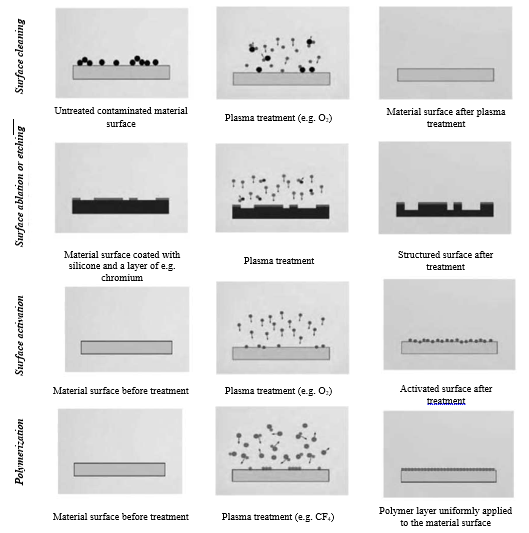
Figure 1 Schematic diagram of plasma action on substrate surface
Source:
S. ERCEGOVIĆ RAZIĆ, R. ČUNKO: Modification of textile properties using plasma, Textile 58 (3) 55-74 (2009), A Review https://platform.ict-tex.eu/pluginfile.php/4110/mod_book/chapter/77/Textile_2009_Review.pdf
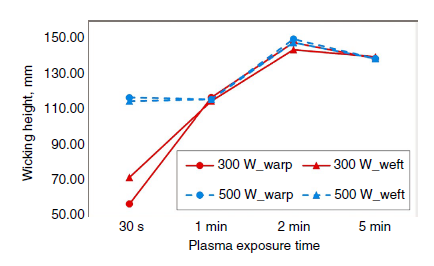
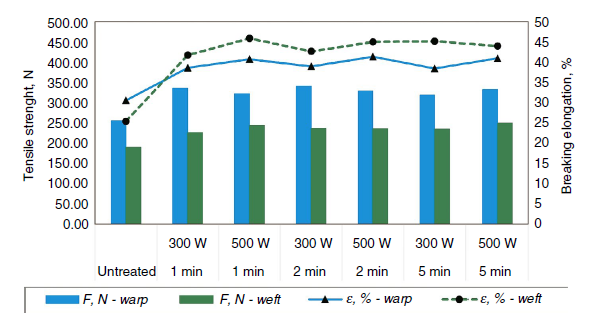
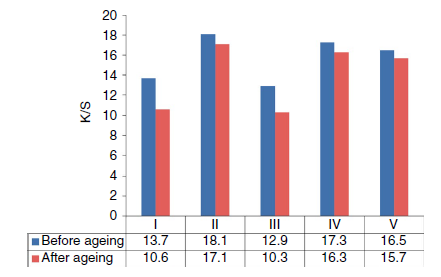
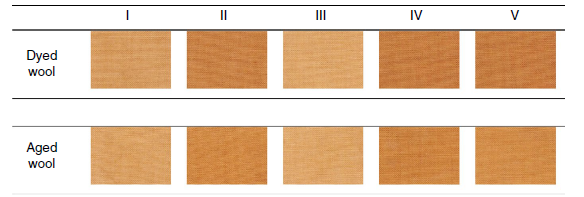
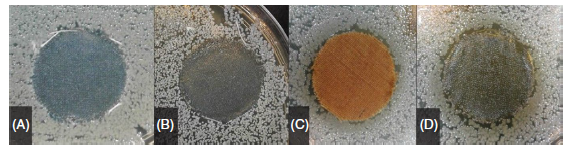