2. New technologies for textile functionalization
2.8. Biotechnological treatments
Biotechnological treatments
Disadvantages of enzymes: poor stability, poor compatibility with other chemical agents, longer processing time, relatively high cost.
Today, using of biomolecules is promising for treatment of synthetic fibers.
Group of researchers are used Polylysine (PLL ) biomolecule - as a surface coating agent for simultaneously imparting hydrophilic and antibacterial functions to PA fiber.
It well known that polyamide (PA) fiber possess lower hydrophilic properties and poor wearing comfort and without antibacterial function, but in the same time PA fiber is after polyester (PES) fiber, on the second place of applied fiber for production underwear, outerwear, sports/leisure wear and decorative fabrics.
Polylysine biomolecules are used to fabricate PA as material with the hydrophilic and antibacterial surface by a dip coating technique.
Chemical mechanism: The Schiff base reaction between the aldehyde groups of glutaraldehyde (used as crosslinker) and the amino groups of PLL and PA fiber was utilized to increase washing resistance.
Results: Final effects on the hydrophilicity of PA fabric were studied by the wetting time of water droplet, while the coating effect was further confirmed by water contact angle, moisture adsorption and capillary effect tests. The functional surface of the PLL coated fabric was proved by scanning electron microscope, X-ray photoelectron spectroscopy, and charge effect.
Conclusions: The PLL coated fabric exhibited excellent hydrophilic and antibacterial properties with good washing durability. This research suggests that PLL biomolecule can be used as a surface coating agent for imparting hydrophilic and antibacterial functions to PA fiber in the same time.
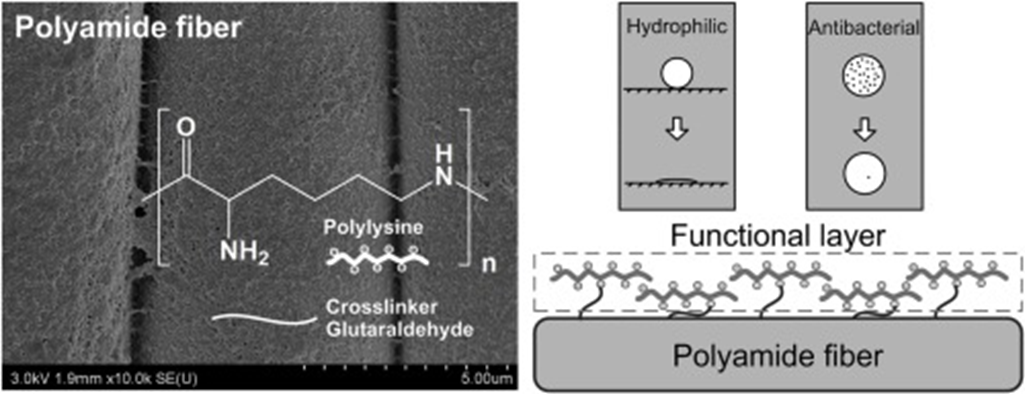
Source: W. Zhank et al.: Progres in Organic Coatings, 142, 2020, 105571, https://doi.org/10.1016/j.porgcoat.2020.105571
Surface of PLA sutures - high hydrophobicity - poor biocompatibility and cellular affinity.
Treatment: PLA sutures were etched by lipase firstly, and then grafted with chitosan - In order to increase the hydrophilicity (number of hydroxyl (-OH) bonds increase),
- the optimal conditions of treating PLA sutures by lipase were as follows: 45 Celzius degree reaction of temperature, 4.5 g/L concentration of lipase and 8 h reaction time.
- the optimal conditions of grafting chitosan onto PLA sutures were as follows: 4 h reaction time and 3 g/L concentration of chitosan. The chitosan grafted and loaded on the surface of PLA sutures, and in some areas of the sutures which led to a rough surface and large friction coefficient.
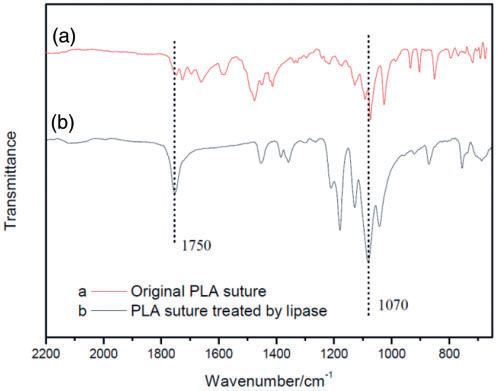
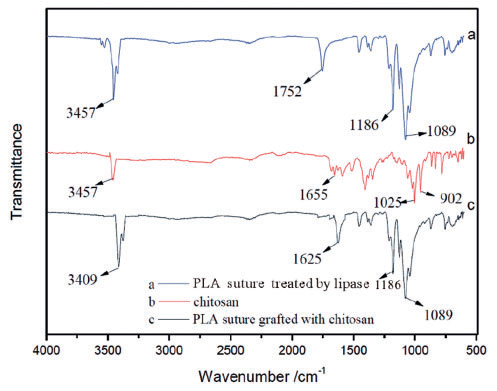
Fig. 2.8.2. FTIR: (a) original PLA suture; (b) PLA suture treated by lipase. Fig. 2.8.3. FTIR: (a) PLA treated by lipase; (b) chitosan, (c) PLA grafted with chitosan.
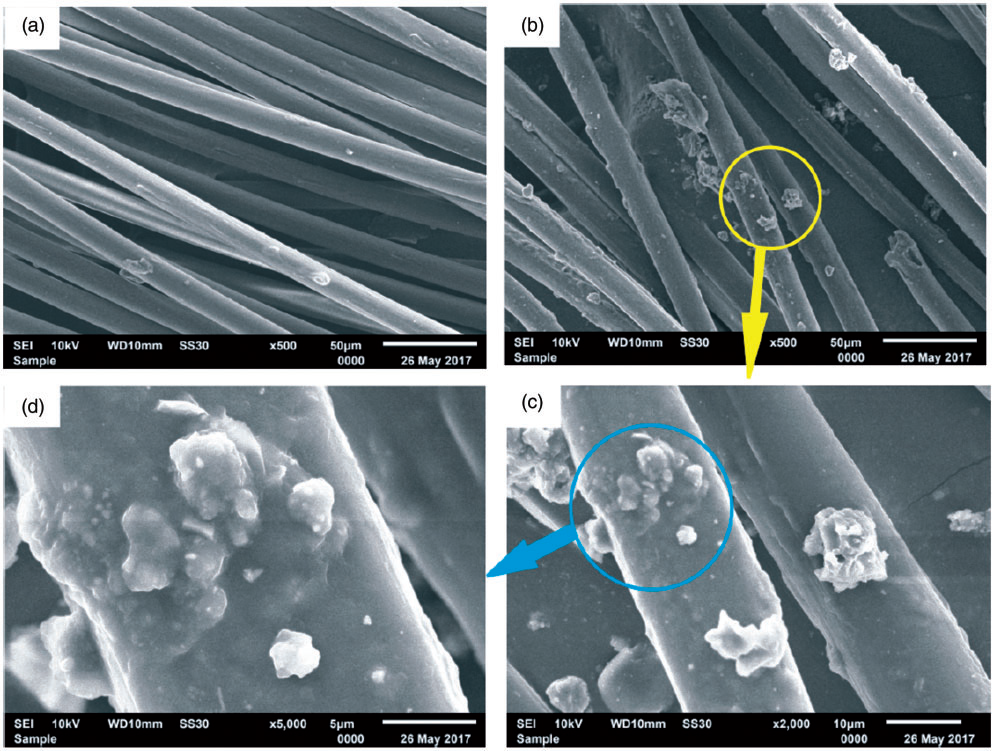
Fig. 2.8.4. SEM images of polylactic acid (PLA) sutures: (a) original PLA sutures; (b) PLA sutures grafted with chitosan (x500); (c) PLA sutures grafted with chitosan (x2000); (d) PLA sutures grafted with chitosan (x5000).
Source: Textile Research Journal 2019, Vol. 89(16) 3291–3302, sagepub.com/journals-permissions DOI: 10.1177/0040517518811936
Enzymatic Bleaching
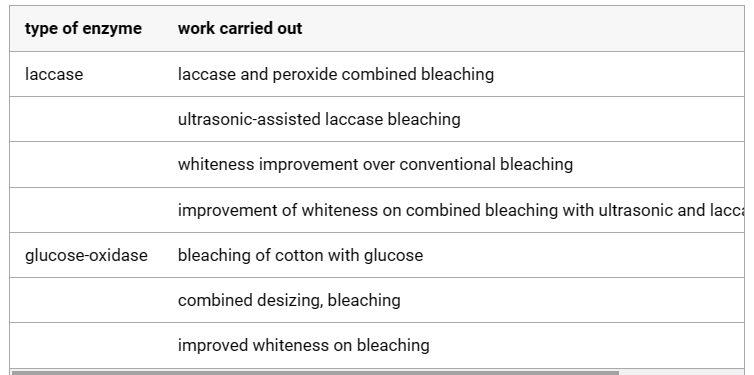
- Choudhury, A. K. R. Environmental Impacts of Denim Washing, Muthu, Subramanian Senthilkannan-Sustainability in Denim. In The Textile Institute Book Series; Woodhead Publishing, 2017; pp 49– 81. DOI: 10.1016/B978-0-08-102043-2.00003-4.
- Liu, X.; Kokare, C. Microbial Enzymes of Use in Industry. In Biotechnology of Microbial Enzymes; Brahmachari, G., Ed.; Academic Press, 2017; pp 267– 298. DOI: 10.1016/B978-0-12-803725-6.00011-X.
- Madhu, A.; Chakraborty, J. N. Developments in Application of Enzymes for Textile Processing. J. Clean Prod 2017, 145, 114– 133, DOI: 10.1016/j.jclepro.2017.01.013.