Other novel multifunctional applications for superhydrophobic textiles including: also UV-blocking, photocatalytic, flame-retardant, asymmetric superhydrophobic/superhydrophilic, and stimuli-responsive, which represent potentially high value-added textiles that can be realised by relatively simple chemical treatment, with special attention to research on environmentally friendly preparation methods, durability and mechanical stability of treated textiles.
There are several techniques for fabrication of superhydrophobic textile surfaces (mentioned through chapters) with two relevant factors: a) the appropriate hierarchical structure with durable micro/nanoparticles and b) a low energy surface:
- for micro-scale fibre structure - coating of nanoscale particles onto the fibre surface to achieve the micro/nanoscale structure and post-fluorinate the hierarchical structure for the low energy;
- methods for preparing superhydrophobic textile surfaces include physical and chemical approaches, such as dip-coating, wet chemical deposition, electro-assisted chemical deposition, spraycoating, sol–gel, chemical etching, chemical vapour deposition, plasma processing, and polymer grafting.
These available fabrication technologies could be divided through the categories: (i) pre-roughening and post-fluorinating - most common methods in preparation of cellulose-based superhydrophobic textile surfaces:
- functionalization with nanoparticles or nanofillaments or a layer of film for achievement of the required roughness, nanoparticles such as
SiO2, TiO2, and ZnO to generate a roughness and durable superhydrophobic surface, as well as some inorganic or organic chemical
materials to fabricate superhydrophobic cellulose-based surfaces.
Example of sequential roughening/lowering surface energy treatment:
Dip-coating method - superamphiphobic fabric with a significant self-healing effect against both physical and chemical damages via a two-
step wet chemical route: the cleaned fabric is immersed in a fluoroalkyl surface-modified silica nanoparticle solution for
5 minutes and coated in fluorinated decylpolyhedral oligomeric silsesquioxane (FD-POSS) and fluoroalkylsilane (FAS) solution. The surface of polyester fabric exhibits a distinct protrusion structure after coating, and fabric surface showed
considerable liquid repellence to liquids with various surface tension and the Contact Angle remained above 150 degrees (for tested liquid of surface tension greater than 22.1 mN/m (Fig. 3.2.3.d).
Fig. 3.2.3. (a) Chemical structures of coating materials and procedure for coating treatment. SEM images of (b) uncoated and (c)
coated polyester fibres. The relationship of the CA (d) and SA (e) with surface tension and the CA changes of water, hexadecane and
ethanol with time (f).
- another study for enhanced stability superamphiphobic cotton fabric, was realised by immersion of cotton fabricin in chitosan
aqueous solution to anchor amino groups onto cotton fibre. After that deposition with silica nanoparticles was done. A robust
structure was achieved by alternately depositing ormosil clusters onto a chitosan pre-coated cotton surface. Finally, the
superamphiphobic cotton fabric was constructed by modifying with perfluorodecyltriethoxysilane (PFDTES) to lower the surface energy, and displays excellent anti-wetting properties. The superamphiphobic cotton fabric shows high contact angles
arround 160 degrees corresponding to water, cooking oil and hexadecane, and the water droplet and cooking oil can easily
roll off from the cotton surface due to the extremely low adhesion of the cotton surface coating (Fig. 3.2.4.b).
Fig. 3.2.4. (a) Schematic of the fabrication process for superamphiphobic cotton fabrics, (b) Photographs of water, cooking oil and
hexadecane droplets on the coated cotton fabrics.
(ii) simultaneous roughening and fluorinating (one-pot method) - this strategy is by one-step dipping the samples into an appropriate pre-fluorinated micro-polymer or micro/nanoparticle solution, or sol–gel solution. Compared to the previous technology (i), the one-pot method takes less time and is potentially cost-saving, and can be more easily used in large scale application.
Wetting chemical coating - for chemically stable superamphiphobic fabric prepared via a one-pot wetting coating method using a coating solution containing poly(vinylidenefluoride-cohexafluoropropylene) (PVDF-HFP), fluoroalkylsilane (FAS) and a volatile
solvent (acetone) (Fig. 3.2.5. a-c). The coated fabric exhibit super-repellent to liquids with a surface tension greater than 21.5 mNm-1 in acetone solution (Fig. 3.2.5.d), and showed good stability under continued liquid dropping with
the static contact angle unchanged. The solution system of PVDF-HFP has a significant impact on super- amphiphobicity and the threshold surface tension of coating to various liquids, while the fabric treated with DMF– acetone solution, the surface tension threshold is 30 mNm-1 while the value changes to 32 mNm-1 when DMF was
used as the solvent. Comparing SEM images before and after the coating treatment, the pristine polyester fibre had
a smooth surface while a rough morphology was formed on the treated polyester fibre no matter which solution system was adopted (Fig. 3.2.5. e and f).
Coating surface exhibited high stability against the extreme conditions (such as 98% H2SO4, 40% NaOH), physical
abrasion for 1000 cycles and machine wash for at least 800 cycles, and such super-strong, superamphiphobic coating
surface is useful for developing functional and innovative clothing surfaces.
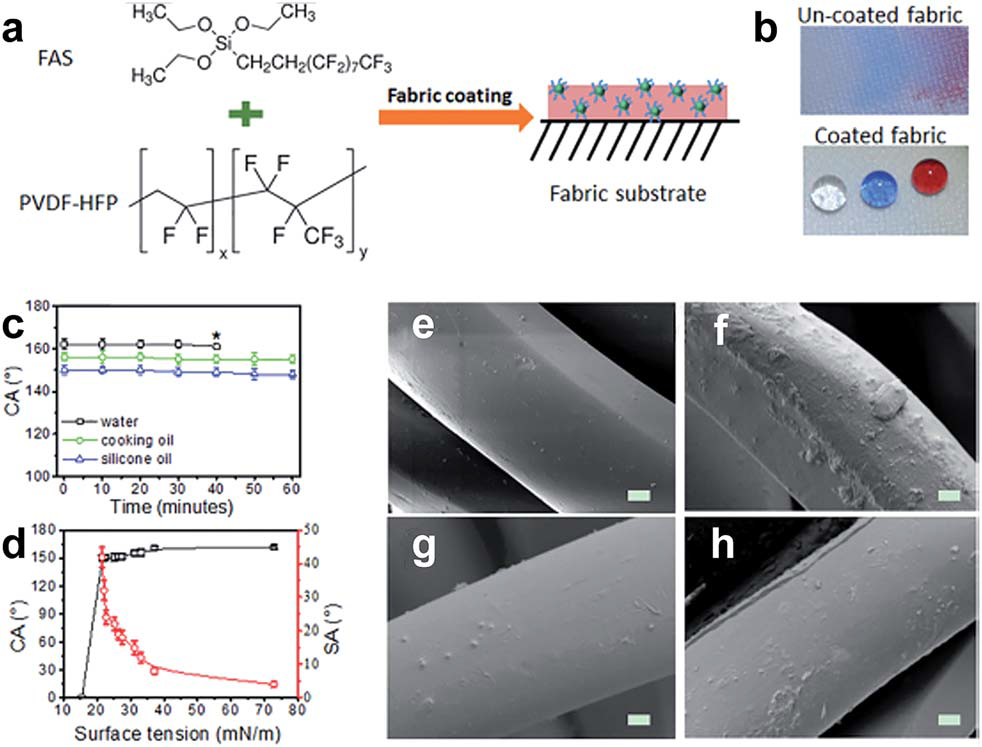
Fig. 3.2.5. (a) Chemical structures of coating materials and procedure for coating treatment,
(b) water, olive oil, and silicone oil drops on the uncoated fabric and the coated fabric, (c) CA change
with time (* is the point when the liquid drop evaporated over) and (d) dependency of the CA and SA
on the surface tension of liquids. SEM images of polyester fibre (e) uncoated, (f) coated in DMF-based
coating solution, (g) coated in DMF/acetone (v/v = 1 : 1) based coating solution, and (h) coated in acetone-
based coating solution (all coated fabrics were dried at 135 oC for 30 min).
Other similar approaches beside chemical coating, include chemical vapour deposition, electrochemical deposition, layer by layer self-assembly
and so on.
Multifunctional applications - increasing demands for multifunctional advanced materials with super-antiwetting properties, great
attention is focused on special wetting surfaces for a large number of functional applications. Most prominently, special wetting
surfaces are regarded as excellent oil/water separation materials due to the different wettability to water and oil, such as being
superhydrophobic and superhydrophilic, superoleophilic and superoleophobic.
Textiles with a textured structure are very easily attacked by various chemical solvents (acid, base, salt, organic and inorganic solution) and lose their intrinsic properties. Superhydrophobic textiles fabricated by constructing appropriate surface roughness and suitable chemistry have
been successfully demonstrated for a range of applications, such as oil/water separation, self-cleaning, and multifunctional materials containing UV-shielding, flame-retardant, anti-icing, and photocatalytic properties, as well as some smart materials with self-healing, stimuli-responsive, patterning and asymmetric response, etc. In this section, we will mainly focus on the functional applications of textiles (mainly on cellulose based materials) with special wettability surfaces.
Superamphiphobic surface
- developed for advanced textiles totally anti-wetting surface, anti-fouling, and packaging materials for precision instruments where anti-wettability is expected for not only pure water but also for some low surface energy solutions (e.g., detergent solution, rain water, underground water, waste water, and sea water) and organic ‘oils’ (e.g., hexane, hexadecane, toluene, mineral oil, and cooking oil).
Treatments - example:
- superoleophobic polyester fabric by coating silicone nanofilaments, followed by plasma fluorination - a fabric surface was revealed to have outstanding repellence against static liquid drops with low surface energy and exhibited a possible highest oil-repellence grade of eight.
- superoleophobic woven fabric with a multilength scale structure by adding two layers of silica particles (microparticles and nanoparticles) on the woven structure. Subsequently, the multi-length scale roughness fabric was incorporated with fluoroalkyl groups to obtain superoleophobic
properties. The modified woven fabric demonstrated a high hexadecane static contact angle (153o for 5 mL droplets) and low roll-off angle (9o for 20 mL droplets).
- new coating system for durable self-healing superamphiphobic fabric surface via a two-step dip coating method (Fig. 3.2.6. b) with two coating solutions, one consisting of nanoparticle silica sol and FAS in ethanol under alkaline conditions, and the other a fluoro-containing polymer, poly(vinylidenefluoridehexafluoropropylene) (PVDF-HFP) dispersed in dimethylformamide (DMF) solution containing FAS. The coated fabric
showed super-antiwettability and can withstand at least 600 cycles of standard laundry (Fig. 3.2.6. c,d) as well as 8000 cycles of mechanical abrasion without any apparent change in superamphiphobic properties. The coated fabric has self-healing ability with a short-time thermal treatment or long time ageing after exposure to extreme conditions, such as acid/base, ozone and boiling treatment.
Fig. 3.2.6. (a) Chemical structure of FAS and PVDF-HFP. (b) Coating for superamphiphobic fabrics. (c) CA and (d) SA change with laundry cycles.
Self-cleaning/photocatalytic/anti-bacterial
Self-cleaning coatings can be broadly classified into two major types: photocatalysis-induced superhydrophilic coatings and superhydrophobic or superamphiphobic coating.
Superamiphobic or superamphiphobic surfaces - air layer gets trapped between the nano/microstructure and water droplet, resulting in the formation of a composite air/liquid/solid interface and increase in the contact angle. A liquid droplet can easily roll off from the fabric surface and take away the surface dirt.
Superhydrophilic coatings - surface is cleaned by exerting the photocatalytic effect which breaks down the organic substances into carbon dioxide and water. The selfcleaning property of super-antiwetting fabric is summarized as three types: physical self-cleaning, chemical self-cleaning and biological self-cleaning.
Physical self-cleaning is mainly mimicking the lotus leaf surface and characterized by measuring the water contact angle and the sliding angle.
- self-cleaning cotton fabric surface coated with a superhydrophobic and superoleophobic thin composite polymer film consisting of modified SiO2 nanoparticles and a fluoropolymer.
Chemical self-cleaning refers to the degradation of the colour stain or pollution solution using the photocatalytic effect.
- the physical selfcleaning process is unable to clean oil pollutants if the surface is superhydrophobic and oleophilic, incorporation of
ZnO or TiO2 nanoparticles becomes indispensable to degrade organics by the photocatalytic effect.
- is developed a photocatalysis-induced self-cleaning polyester non-woven fabric surface by dip-coating a fluorine-free low surface energy
polybenzoxazine (PBZ) solution with TiO2 nanoparticles, followedby thermal treatment. The oil droplet on the treated fabric surface can be photodegraded by TiO2 endowing the fabric with self-cleaning performance
- new covalently immobilize TiO2 nanoparticles onto the fabric surface by grafting polymerization of 2-hydroxyethylacrylate (HEA) under γ-ray irradiation - functional fabric showed photocatalytic self-cleaning performance when using oleic acid dyed with oil red as the organic stain.
The biological self-cleaning corresponds to antibacterial activity of functional fabric against a Gram-positive bacterium (Staphyloccocus
aureus) and a Gram-negative bacterium (Escherichia coli).
- biomimetic method to construct nanostructured Ag@ZnO on the cotton fabric surface; such flexible fabrics exhibited not only visible-light driven photocatalysis but also anti-bacterial activity against Gram-positive bacteria and Gram-negative bacteria
Asymmetric/patterning/stimuli-responsive
Durability/self-healing/UV-shielding/flame-retardant
👉 Source: Review paper - J. Mater. Chem. A, 2017, 5, 31–55, DOI: 10.1039/c6ta07984a